Plywood is a cornerstone material in construction, furniture making, and countless other industries. Its remarkable combination of strength, stability, and adaptability makes it a go-to choice for builders, designers, and manufacturers worldwide. But what exactly makes plywood so special? This article delves into the world of plywood, exploring its various types of plywood, key plywood properties, inherent durability, and incredible versatility. Whether you're a seasoned construction professional like Mark Thompson, a building material supplier, or a furniture maker, understanding the nuances of plywood is crucial for selecting the right material for your needs and ensuring project success. Join us as we uncover why plywood remains an indispensable engineered wood product.
What Exactly is Plywood and How is it Made?
At its core, plywood is an engineered wood product constructed from multiple thin layers, or "plies," of wood veneer. These thin sheets are glued together under heat and pressure. The critical aspect of how plywood is made lies in the orientation of these veneers. Each layer's grain direction is typically rotated 90 degrees relative to the adjacent layer. This cross-graining technique is fundamental; it gives plywood its strength, stability, and resistance to splitting, which are significant advantages over solid lumber.
The process to make plywood involves several steps: selecting logs, peeling them into thin veneers, drying these veneers to a specific moisture content (crucial for preventing warping later), grading and sorting the veneers, applying adhesive, laying up the veneers in the cross-grained pattern, pressing the assembly under heat, and finally trimming and sanding the finished plywood panels. The type of wood used (hardwood or softwood), the adhesive type, and the quality of the veneers all influence the final characteristics and plywood properties. As a manufacturer, we pay close attention to each stage, especially moisture control and lamination quality, to ensure consistent, high-quality plywood.
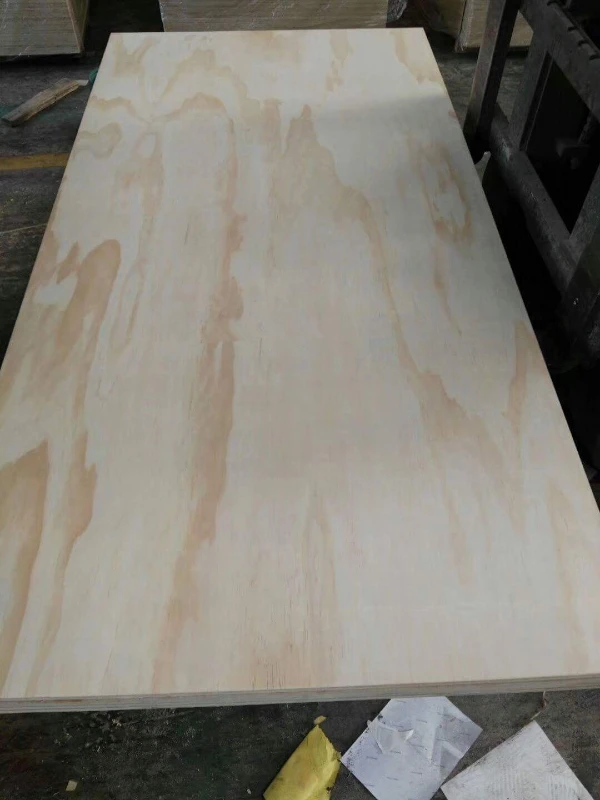
What are the Key Properties That Make Plywood So Useful?
The key properties of plywood stem directly from its unique layered construction. Firstly, plywood offers strength and stability in multiple directions, unlike solid wood which is strongest along the grain. This cross-lamination distributes stress effectively, making plywood highly resistant to bending, warping, twisting, and shrinking. This dimensional stability is vital in construction where materials are exposed to varying temperatures and humidity levels. Plywood properties also include excellent impact resistance.
Secondly, plywood exhibits a high strength-to-weight ratio. Plywood is strong yet relatively lightweight compared to solid timber of similar dimensions, making it easier to handle, transport, and install on job sites. Furthermore, plywood can be easily cut, drilled, and shaped using standard woodworking tools, offering great workability. Depending on the type of plywood and adhesives used, it can also possess significant resistance to moisture and chemicals. These combined characteristics of plywood make it incredibly versatile for a vast range of applications.
Are There Different Common Types of Plywood?
Yes, plywood comes in many forms, tailored for specific uses. The common types of plywood are often categorized based on the wood species used (hardwood, softwood), the type of adhesive (interior or exterior), the intended application (structural, general purpose), or special treatments (marine-grade, fire-retardant). Understanding these plywood types is essential for making informed purchasing decisions.
Some basic categories include:
- Softwood Plywood: Made from coniferous trees like pine, fir, or spruce. Often used in construction for framing, sheathing, and subflooring.
- Hardwood Plywood: Made from deciduous trees like oak, birch, maple, or poplar. Valued for its strength, smooth surface, and aesthetic appeal, making hardwood plywood suitable for cabinets, furniture, and decorative paneling.
- Exterior Plywood: Uses water-resistant adhesives (like phenol-formaldehyde) allowing it to withstand moisture and weather exposure.
- Interior Plywood: Uses less water-resistant adhesives (like urea-formaldehyde) and is suitable for dry, indoor applications.
- Structural Plywood: Engineered and tested to meet specific strength and stiffness requirements for load-bearing applications in construction.
- Marine Plywood: A high-performance plywood made with waterproof glue and high-quality veneers, designed to endure prolonged exposure to moisture.
Hardwood vs. Softwood Plywood: What's the Difference?
The primary difference lies in the source wood. Hardwood plywood is manufactured using veneers from deciduous trees (which lose their leaves seasonally), while softwood plywood is made from coniferous trees (evergreens with needles). This fundamental difference impacts their properties and common uses. Hardwood plywood, often using species like birch, oak, or poplar, is generally denser, harder, and has a smoother surface finish. This makes plywood is ideal for furniture, cabinetry, flooring, and architectural millwork where appearance and durability are key.
Softwood plywood, typically made from pine, fir, or spruce, is usually lighter in weight and more economical than hardwood plywood. While not as dent-resistant, softwood plywood typically offers excellent structural strength and stiffness, making it a workhorse in construction for sheathing, roofing, subfloors, and general utility purposes. Softwood plywood is typically used where structural performance outweighs aesthetic finish. However, higher grades of softwood plywood can be sanded plywood, providing a surface suitable for painting or basic finishing.
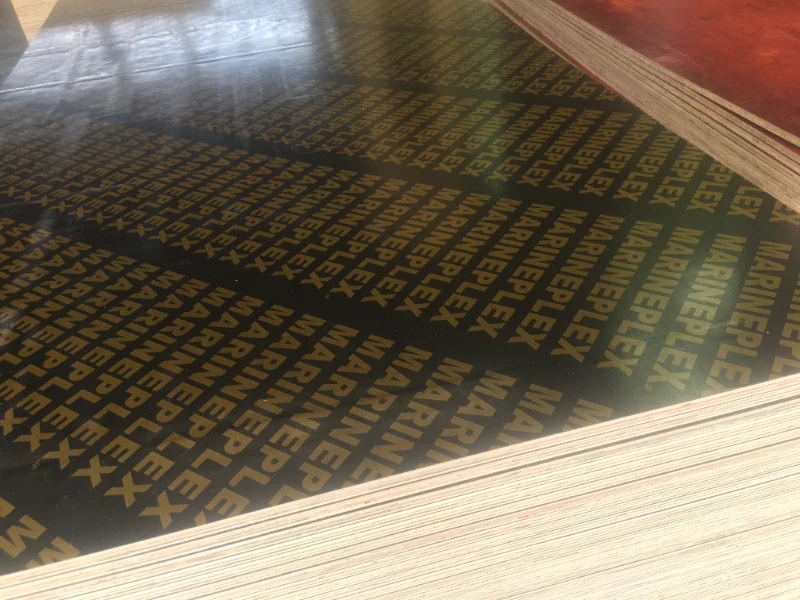
Diving Deeper: Specialized Plywood Types (Marine, Structural, Film-Faced)
Beyond the basic hardwood/softwood distinction, several specialized plywood products cater to demanding applications:
-
Marine Plywood: This isn't just exterior plywood. True marine plywood uses highly water-resistant adhesives (typically WBP - Weather and Boil Proof) and is made from durable hardwood veneers with minimal core gaps. This construction prevents water from penetrating the layers, making marine plywood ideal for boat building, docks, bathroom subflooring, and other applications requiring extreme moisture resistance and durability. It's designed to resist fungal attack and delamination even in wet conditions.
-
Structural Plywood: This type of plywood is designed specifically for load-bearing applications in building construction. Structural plywood is manufactured and tested according to strict building codes and standards (like AS/NZS 2269 in Australia). It carries specific stress grades (e.g., F8, F11, F17) indicating its structural capacity. Plywood in construction, particularly structural plywood, is used for bracing, flooring, roofing, and engineered beams, where predictable strength and performance are critical. We ensure our structural plywood meets these rigorous standards.
-
Film-Faced Plywood (Formply): This plywood features a smooth, resin-impregnated film bonded to one or both surfaces. The film creates a durable, water-resistant finish, ideal for concrete formwork. The smooth surface imparts a fine finish to the concrete and allows for multiple reuses of the plywood panels, making it cost-effective for contractors. Phenolic film faced plywood 16mm is a common example, offering excellent performance in forming applications. Plywood is often chosen for formwork due to this specialized type.
How Strong is Plywood? Understanding Strength and Durability
Plywood is renowned for its impressive strength and durability, largely attributed to its cross-laminated structure. This construction method distributes load across the entire panel, preventing the plywood from splitting along the grain like solid wood can. The strength of plywood is multi-directional, meaning it resists stress applied both along and across the panel face. This bi-directional strength is a significant advantage in structural applications where loads may not always align with the grain.
The durability of plywood depends on several factors: the wood species used (hardwoods are generally more durable than softwoods), the quality of the veneers (fewer knots and voids lead to stronger panels), and crucially, the type of adhesive. Exterior-grade adhesives significantly enhance plywood's resistance to moisture, temperature fluctuations, and biological decay, leading to longer service life, especially in exposed conditions. Certain types of plywood, like marine plywood, are specifically engineered for maximum durability in harsh environments. The inherent strength and stability make plywood a reliable choice for demanding structural and industrial uses.
What are the Main Advantages of Using Plywood?
The advantages of plywood are numerous, contributing to its widespread adoption:
- Strength and Stability: As discussed, the cross-graining provides exceptional dimensional stability and resistance to warping, twisting, and shrinking compared to solid wood. Plywood offers strength in multiple directions.
- High Strength-to-Weight Ratio: Plywood is strong yet relatively light, simplifying handling and installation, potentially reducing structural support requirements and transportation costs.
- Impact Resistance: The layered structure absorbs shocks well, making plywood resistant to impacts and damage.
- Versatility: Plywood can be used for structural framing, sheathing, subflooring, furniture, cabinetry, formwork, decorative paneling, and much more. Its versatility is a key benefit.
- Workability: Plywood can be easily cut, shaped, drilled, and fastened using standard tools.
- Panel Size: Plywood is available in large sheet sizes (e.g., 4x8 feet or larger), allowing for rapid coverage of large areas, reducing joints and installation time.
- Cost-Effectiveness: While initial cost plywood can vary, plywood is generally more cost-effective than solid lumber of comparable dimensions for many applications, especially considering its stability and coverage area. Plywood offers several advantages in terms of project efficiency.
- Surface Finish: Depending on the grade and type (hardwood plywood, sanded plywood), it can offer a smooth, consistent surface suitable for painting, veneering, or laminating.
These combined benefits of using plywood make it a practical and efficient material for diverse projects.
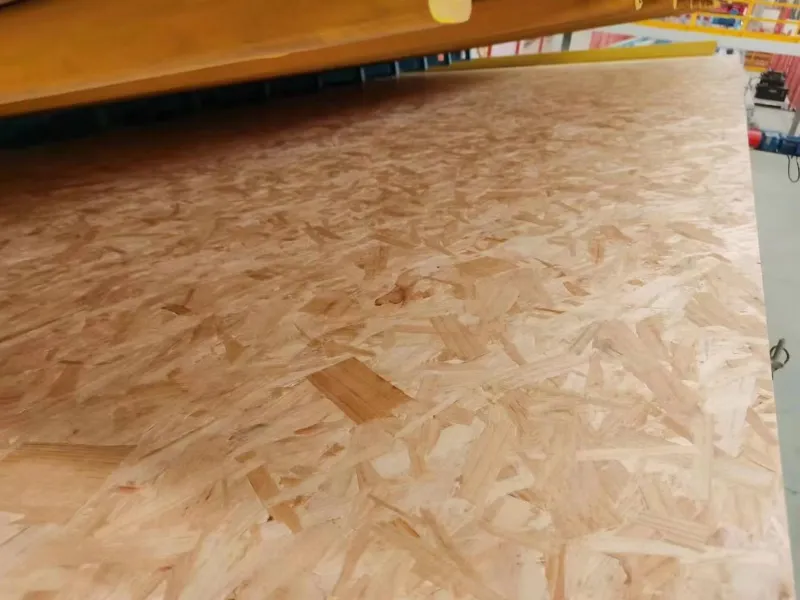
Where is Plywood Most Commonly Used?
The common applications of plywood span across various industries, showcasing its remarkable versatility:
- Construction: This is arguably the largest market for plywood. Plywood is widely used for:
- Wall Sheathing and Roof Decking
- Subflooring
- Structural Bracing (structural plywood)
- Concrete Formwork (film-faced plywood / Formply)
- Hoarding and temporary structures
- Furniture Manufacturing: Hardwood plywood is a staple for carcasses, shelving, drawer bottoms, and backs. Plywood is ideal for furniture components requiring stability and a good finishing surface. Plywood is favored for its stability over solid wood in larger panels.
- Cabinetry: Kitchen and bathroom cabinets extensively use plywood for boxes, shelves, and sometimes even door panels (hardwood plywood).
- Interior Design: Decorative wall paneling, ceiling features, and fixtures often utilize plywood for its aesthetic potential (hardwood plywood) and workability.
- Flooring: Plywood serves as a stable underlayment or subfloor for various finish flooring materials. Specific plywood products are also used as the core for engineered flooring.
- Transportation: Used in flooring, lining, and partitions in trucks, trailers, buses, and RVs due to its strength and durability.
- Marine Applications: Marine plywood is essential for boat hulls, decks, and interior components.
- Packaging: Crates and boxes requiring strength often use utility grades of plywood.
This list highlights just some of the applications of plywood, demonstrating why plywood is a popular choice across so many sectors. Plywood is commonly used due to its reliable performance.
How Do Plywood Grades Affect Quality and Application?
Plywood is graded based on the quality of the face and back veneers, particularly concerning the number and size of defects like knots, splits, patches, and discoloration. Understanding grades of plywood is crucial for ensuring you get the expected appearance and performance. Common grading systems (like the US system using letters A, B, C, D) define veneer quality:
- A-Grade: Smooth, paintable surface. Few, if any, knots or repairs. Used for high-end furniture, cabinets, and architectural applications where appearance is paramount. A-grade plywood represents the highest visual quality.
- B-Grade: Solid surface with minor defects. May have some neat repairs (plugs or patches) and tight knots. Suitable for utility applications or where a less-than-perfect finish is acceptable or will be covered. B-grade plywood offers a balance of quality and cost.
- C-Grade: May have knotholes up to a certain size, splits, and discoloration. Often used for structural purposes where appearance is not a concern, like sheathing or subflooring. C-grade plywood is common in structural plywood.
- D-Grade: Allows larger knots and knotholes. Used for applications where strength is needed but appearance is irrelevant, often for the back face of structural panels or temporary uses.
Plywood typically has two grades indicated (e.g., AC, BC, CDX - X for exterior glue). The first letter is the face veneer grade, the second is the back. Plywood quality directly correlates with these grades. Choosing a higher grade than necessary increases cost, while choosing too low a grade can compromise the finish or structural integrity. As a plywood manufacturer, we clearly label our plywood grades to help customers like Mark make the right selection.
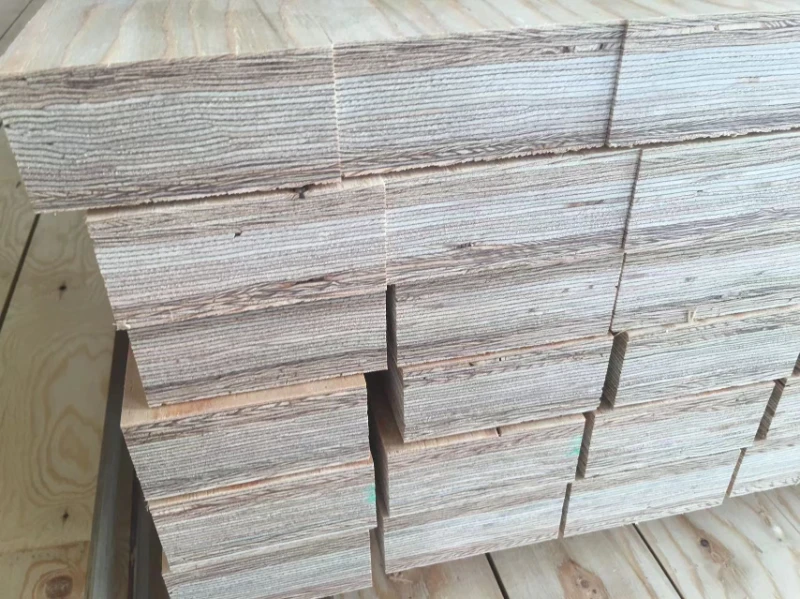
How Do I Choose the Right Plywood for My Project?
Selecting the right plywood involves considering several factors related to your specific application:
- Application Environment: Will the plywood be used indoors or outdoors? Will it be exposed to moisture? For exterior or wet conditions, choose Exterior grade or Marine Plywood. For dry interiors, Interior grade may suffice.
- Structural Requirements: Is the plywood intended for a load-bearing application? If yes, structural plywood with the appropriate stress grade (e.g., F11, F17) is essential. Non-structural plywood is suitable for general purposes like cabinetry, shelving, or non-load-bearing partitions. Check out options like 17mm plywood non structural for these uses.
- Appearance Needs: Is the surface finish critical? For fine furniture or visible architectural elements, A-grade hardwood plywood is often preferred. For surfaces to be painted or covered, a B-grade or C-grade face might be adequate and more economical.
- Required Strength and Durability: Consider the expected wear and tear. Hardwood plywood generally offers better surface durability than softwood plywood. The thickness of plywood also plays a significant role in strength and stiffness – thicker plywood provides greater load capacity. Plywood thickness can vary widely.
- Budget: Higher grades and specialized plywood types (like marine plywood or high-grade hardwood plywood) typically cost more. Balance your performance needs with your budget. Softwood plywood is often a cost-effective choice for structural applications.
- Certifications: For specific markets or projects (especially in the US, Europe, Australia), check for necessary certifications like FSC (Forest Stewardship Council) for sustainability, CARB compliance for formaldehyde emissions, or relevant structural certifications (e.g., AS/NZS).
Carefully evaluating these points will help you choose the right plywood for your specific needs, ensuring both performance and cost-effectiveness. Plywood is a versatile material, but matching the type of plywood to the job is key.
Partnering with a Reliable Plywood Manufacturer: What to Look For
For buyers like Mark Thompson, sourcing plywood from overseas, particularly developing countries like China or Vietnam, requires careful vetting of suppliers. Finding a reliable plywood manufacturer is critical to avoid common pain points like inconsistent quality, inaccurate grading, moisture issues, or delivery delays. Here's what to look for:
- Consistent Quality: A good manufacturer maintains strict quality control throughout the plywood production process, from log selection to final pressing and finishing. Ask about their QC procedures and acceptable tolerances for thickness, dimensions, and defects. Plywood quality should be consistent batch to batch.
- Accurate Grading and Specifications: Ensure the supplier understands and adheres to the grading standards relevant to your market (e.g., US, Australian, European standards). The plywood delivered should match the specifications ordered.
- Verified Certifications: Request copies of relevant certifications (FSC, CARB, structural testing reports like AS/NZS) and verify their authenticity if possible. Reputable suppliers are transparent about their certifications.
- Moisture Content Control: This is crucial. Inquire about their veneer drying processes and target moisture content for finished plywood. Proper control prevents warping, delamination, and mold issues later. Plywood may warp if moisture isn't controlled.
- Communication and Transparency: A reliable partner communicates clearly about production timelines, potential issues, and shipping details. They should be responsive to inquiries and provide necessary documentation promptly.
- Experience and Expertise: Look for manufacturers with experience exporting to your region. They will be more familiar with your market's requirements and logistics. As a factory specializing in plywood and other engineered wood products like LVL and I-Joists for export, we understand these concerns deeply.
- Factory Inspection: If possible, visiting the factory or arranging a third-party inspection can provide valuable insights into their operations and capabilities.
Building a strong relationship with a trustworthy plywood manufacturer like Jsylvl, who prioritizes quality and transparency, is key to mitigating risks and ensuring a smooth supply chain for your projects. We understand the plywood features that contribute to reliable performance.
Key Takeaways on Plywood Versatility
Plywood stands as a remarkably versatile and reliable engineered wood product. Here’s a quick summary of why:
- Engineered Strength: The cross-laminated construction gives plywood its strength, stability, and resistance to splitting and warping.
- Variety of Types: From hardwood plywood for furniture to structural plywood for construction and marine plywood for wet environments, there's a type of plywood for nearly every need.
- Key Properties: High strength-to-weight ratio, impact resistance, workability, and availability in large panels are significant advantages of plywood.
- Wide Applications: Plywood is used extensively in construction, furniture, cabinetry, transportation, packaging, and more, highlighting its immense versatility.
- Grading Matters: Understanding plywood grades (A, B, C, D) helps match the panel's appearance and quality to the application's requirements.
- Informed Selection: Choosing the right plywood involves considering the environment, structural needs, appearance, required durability, budget, and necessary certifications.
- Supplier Reliability: Partnering with a reputable plywood manufacturer ensures consistent plywood quality, accurate specifications, and reliable delivery, mitigating risks for buyers.
By understanding the different types of plywood, their unique plywood properties, and how to select the appropriate grade, you can leverage the full potential of this essential building material for successful and durable projects.
Post time: Mar-26-2025