This article dives deep into the world of plywood, exploring the crucial difference between structural and non-structural options. Whether you're a seasoned construction professional like Mark Thompson, a procurement officer, or simply a DIY enthusiast, understanding this distinction is vital for ensuring the success and safety of your projects. We'll explain why this article is worth reading by providing clear, practical information, expert insights, and real-world examples that will empower you to make informed decisions when choosing the right plywood for your needs.
1. What is Plywood, and Why are There Different Types?
Plywood is one of the most versatile engineered wood products available on the market. It's created by layering thin sheets of wood veneer, called plies, and bonding them together with adhesive under heat and pressure. This cross-graining process – where each ply's grain runs perpendicular to the adjacent layer – is what gives plywood its exceptional strength, stability, and resistance to warping and splitting compared to solid wood.
However, not all plywood is created equal. When it comes to plywood, there are two main categories, different types of plywood: structural and non-structural plywood. The main difference between structural and non-structural lies in their intended use and, crucially, the type of glue used in their construction. These differences dictate where and how each type of plywood should be employed to ensure safety and longevity. Purchasing plywood requires understanding these nuances.
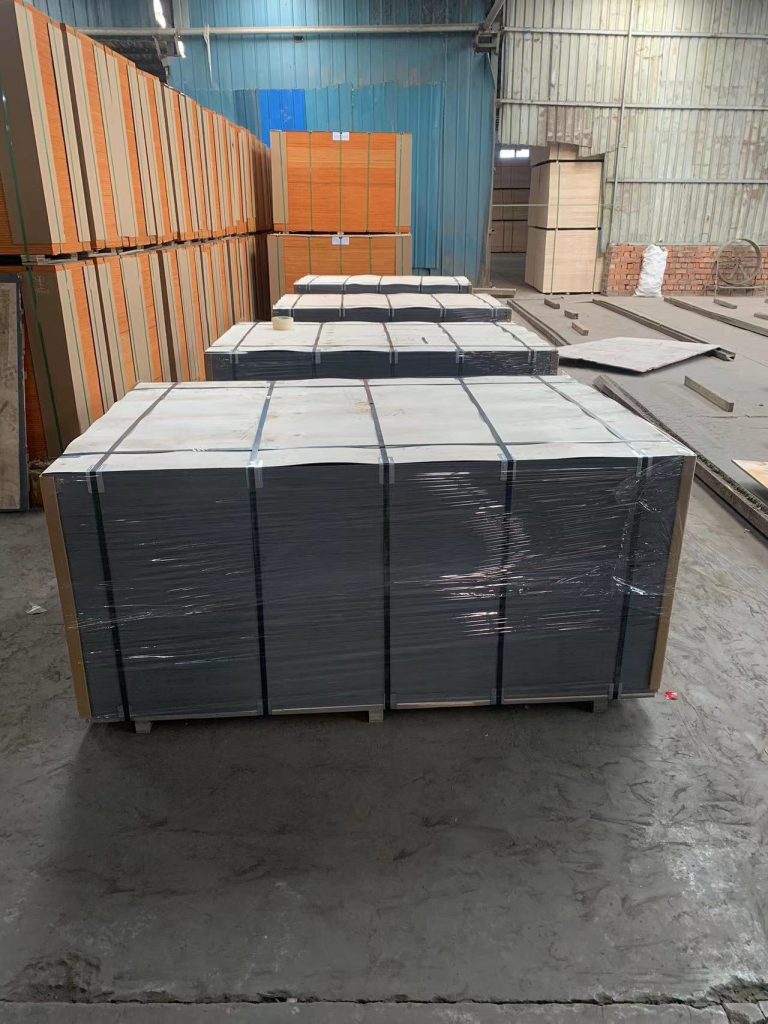
2. What is Structural Plywood? Defining Features and Applications.
Structural plywood is specifically engineered to bear loads and provide structural support in construction. It's designed for applications where strength and stability are paramount, such as:
- Flooring: Providing a solid and stable base for various flooring finishes.
- Roofing: Creating a robust and weather-resistant roof deck.
- Wall Sheathing: Adding rigidity and strength to wall frames.
- Beams and Headers: Forming load-bearing elements in the building's structure.
- Formwork: Creating temporary molds for concrete (using specialized formply, like Formply F17 2400×1200×17mm).
Structural plywood is used to create roof and plywood flooring. These plywood boards adhere to strict manufacturing standards and are typically certified by relevant building authorities. This certification guarantees their performance and suitability for load-bearing applications. Structural plywood is made with glues that are designed to withstand exposure to moisture and temperature changes without delaminating. This is crucial for maintaining the structural integrity of the building.
3. What Makes Plywood "Suitable for Structural" Applications?
The key factor that makes a plywood board "suitable for structural" use is the type of glue that bonds the veneers together. Glues are used for structural plywood that is designed to resist delamination (separation of the layers) under stress and exposure to moisture. The most common adhesive used is a phenol-formaldehyde resin, which creates an A-bond.
- A-Bond: This is the most durable bond, typically achieved using phenol-formaldehyde resin. A-bond plywood can withstand prolonged exposure to wet conditions, including continuous boiling, without delaminating. This makes it ideal for exterior and high-humidity applications. Want the best structural plywood? Look for A-Bond.
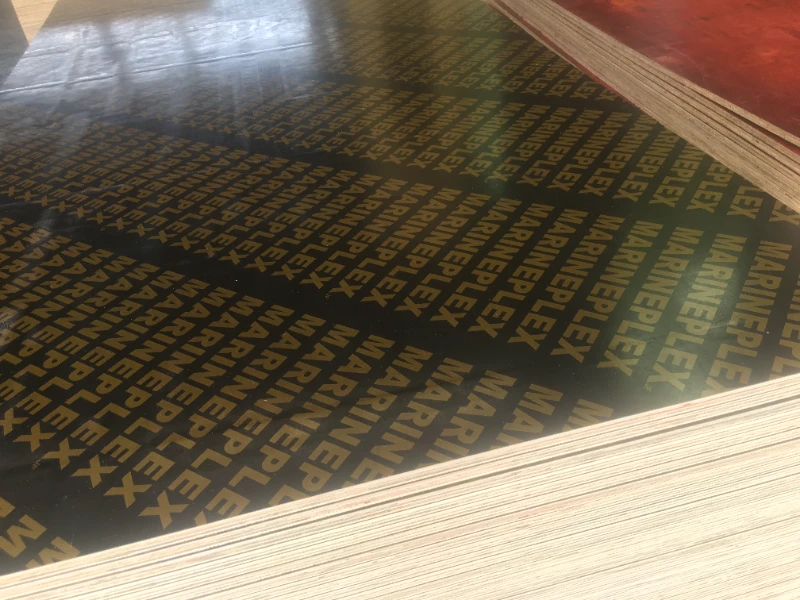
A special type of structural plywood, a type of structural plywood called structural plywood called marine grade, or plywood called marine grade plywood, is made with an A-bond and even higher-quality veneers, offering superior water resistance. The crucial aspect of used for structural plywood and what structural plywood is used for is directly tied to the adhesive strength. For instance, marine plywood is made with a specific type of glue.
It is a fact that the main difference between the two is that A-bond is more durable.
4. What is Non-Structural Plywood? Where is it Best Used?
Non-structural plywood is the type of plywood designed for applications where structural strength is not a primary requirement. While it still possesses good dimensional stability, it's not intended to bear significant loads. Common uses include:
- Interior Paneling: Providing a decorative finish for walls and ceilings.
- Furniture Making: Constructing cabinets, shelves, and other furniture components.
- Underlayment: Creating a smooth surface beneath flooring materials (in dry conditions).
- Packaging and Crates: Providing a lightweight and cost-effective solution for protecting goods during transport.
Non-structural plywood may look great aesthetically, but it lacks the structural support features necessary for load-bearing applications. Using it in place of structural plywood can compromise the safety and integrity of a structure.
5. The Main Difference Between Structural and Non-Structural Plywood: The Glue.
As highlighted earlier, the primary difference between structural and non-structural plywood boils down to the glue. While structural plywood utilizes A-bond adhesives (phenol-formaldehyde), non-structural plywood typically employs B-bond, C-bond, or D-bond adhesives, often based on urea-formaldehyde resin.
- B-Bond: Offers moderate moisture resistance, but its strength is more limited than the A-bond. B-bond glues are used in some exterior applications where exposure to moisture is limited. While B-bond plywood boards can withstand some moisture. B-bond is still is less durable than its A counterpart.
- C and D-Bond: C-bond plywood board, and especially, C-bond type plywood; and D-bond plywood, and especially, D-bond plywood boards Offer the least moisture resistance and are only suitable for interior applications in dry conditions. These glues are not designed to withstand prolonged exposure to high humidity or wet conditions. D-bond plywood is unsuitable for structural uses.
The type of glue used directly impacts the plywood's ability to resist delamination and maintain its strength over time, especially when subjected to high humidity or wet conditions. Non-structural plywood is made with these less water-resistant glues, making it inappropriate for creating structural support. The difference between structural plywood and non-structural one is in the glue.
6. Understanding Plywood Grades: A, B, C, and D.
Beyond the bond type, plywood is also graded based on the appearance and quality of the face and back veneers. The grades range from A (highest quality) to D (lowest quality).
- A-Grade: Smooth, sanded surface with minimal defects. Suitable for applications where appearance is important.
- B-Grade: Solid surface with minor repairs and imperfections.
- C-Grade: May have knots, knotholes, and other defects.
- D-Grade: Allows for larger knots and defects.
It's important to note that the veneer grade plywood refers primarily to the appearance of the plywood, not necessarily its structural capacity. A structural plywood panel can have a C or D face and still be perfectly suitable for structural applications, as long as it has the correct bond type (A-bond). Conversely, an A-grade interior plywood panel with a D-bond is not suitable for structural use, regardless of its beautiful appearance. So it is very important to understand, what type of plywood can also be used.
7. How Does Marine Grade Plywood Fit into the Structural vs. Non-Structural Debate?
Marine grade plywood is a special type of structural plywood designed for extreme moisture exposure. It always uses an A-bond adhesive and is constructed with high-quality veneers with minimal core gaps. This combination makes it exceptionally resistant to water damage and delamination.
It's crucial to understand that "marine grade" doesn't automatically mean it's suitable for all marine applications. While it can withstand hours of continuous boiling without delaminating, the specific application (e.g., boat hull construction) may require additional treatments and certifications.
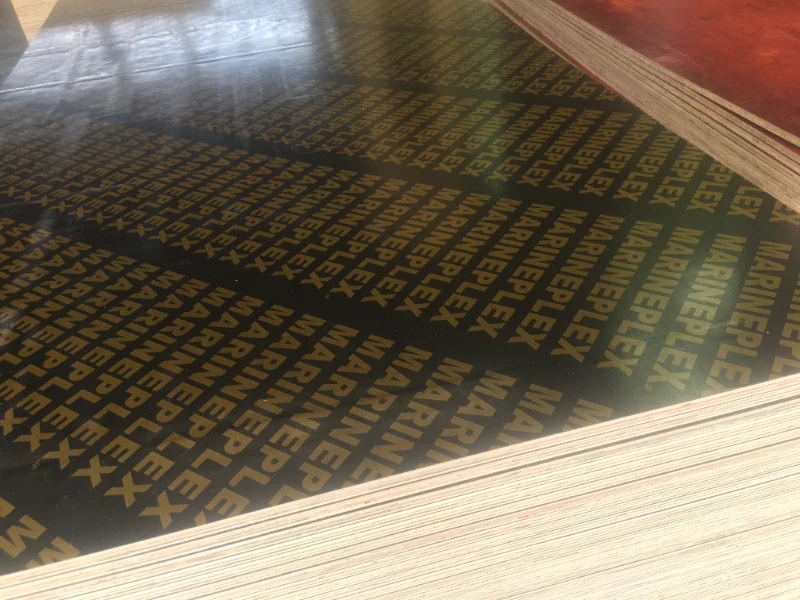
Marine plywood is typically used in:
- Boatbuilding (though specific grades and treatments may be required)
- Exterior applications with constant exposure to water
- High-humidity environments
8. Can Non-Structural Plywood Ever Be Used in Structural Applications?
The short answer is: generally, no. Using non-structural plywood in a structural application is risky and can lead to structural failure. However, there might be extremely limited exceptions, only under the guidance of a qualified structural engineer and with full compliance with local building codes. These exceptions would likely involve very specific, low-load situations where the plywood is not providing primary structural support. This should be seen like rare situation, you should remeber: Non-structural plywood may look nice but is not designed for structural purposes.
For example, a small piece of non-structural plywood might be used as a spacer or filler in a non-critical area, but it should never be used as a substitute for structural plywood in load-bearing elements like beams, floor joists, or wall sheathing.
9. Choosing the Right Plywood: Key Considerations for Your Project.
Selecting the right plywood can be challenging, but these are the most important factors:
- Identify the Application: Is it structural or non-structural? Will the plywood be exposed to moisture?
- Choose the Correct Bond Type: A-bond for structural and exterior use; B, C, or D-bond for interior, non-structural applications.
- Select the Appropriate Grade: Consider the appearance requirements of your project.
- Check for Certifications: Ensure the plywood meets relevant building codes and standards for your region. (FSC, CARB compliance).
- Determine size of plywood board: Do you use for what purpose boards 4x8, 9mm, 12 mm, 18mm or other?
- Consider the Source: Choose a reputable supplier like Jsylvl that can provide quality products and documentation.
10. Where Can I Source High-Quality Structural and Non-Structural Plywood? (Focus on Jsylvl).
Jsylvl, based in China, is a leading factory specializing in engineered wood products, including a variety of structural and non-structural plywood options. We offer:
- LVL Timber (Engineered Wood Products): High-strength, dimensionally stable LVL beams, laminated veneer lumber LVL beams E13.2.
- LVL For Doors: Specifically designed for door core and frame applications.
- Film Faced Plywood: Durable, reusable plywood for concrete formwork, such as 12mm Film faced plywood.
- Structural Plywood: Meeting stringent structural standards for various applications.
- Non-Structural Plywood: Available in various grades and thicknesses for interior use.
- Formply: Formply F17 1800×1200×17mm High-quality formwork plywood for concrete construction.
- OSB Board: Cost-effective alternative for sheathing and other applications.
- Floor: Engineered flooring solutions, including oak and solid wood options.
- SPC Wall Panel: Durable and waterproof wall paneling.
- I-Joist: Efficient and strong I-joists for floor and roof construction.
- Higher grade face: for exterior door skins, exterior door skins and concrete applications, the plywood needs a higher grade face veneer on at least one side.
- Outdoor furniture: Plywood used in crafting outdoor furniture should ideally be of structural grade with an A-bond to withstand environmental elements.
- Wall Linings: For wall linings, non-structural plywood with a C or D bond is typically sufficient, assuming the environment is dry.
- Still Suitable: In scenarios where structural plywood is used in non-load-bearing roles, it's still suitable due to its durability, though it may be over-specified.
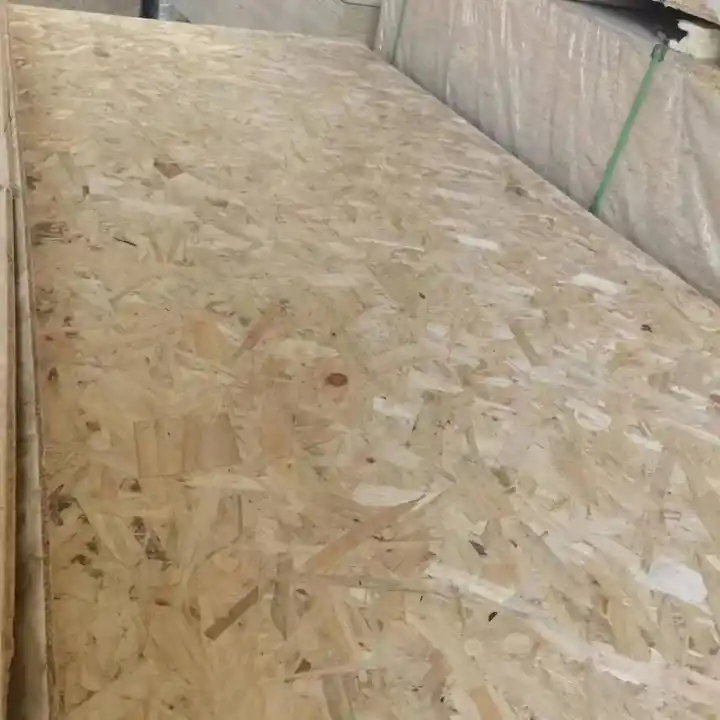
Jsylvl exports to major markets, including the USA, North America, Europe, and Australia. We understand the needs of customers like Mark Thompson, prioritizing quality, competitive pricing, and reliable logistics. Our multiple production lines ensure efficient lead times, and we are committed to providing all necessary certifications to verify the quality and compliance of our products.
We regularly participate in industry exhibitions, providing opportunities to meet our team, inspect our products, and discuss your specific requirements. Contact Allen at Jsylvl to learn more.
Key Takeaways:
- The difference between structural and non-structural plywood lies primarily in the type of glue used.
- Structural plywood uses A-bond adhesives (phenol-formaldehyde) for superior strength and moisture resistance.
- Non-structural plywood uses B, C, or D-bond adhesives (often urea-formaldehyde) and is suitable only for interior, non-load-bearing applications.
- Plywood can also be used to determine structural grade.
- Marine grade plywood is a type of structural plywood with exceptional water resistance.
- Never use non-structural plywood in a structural application unless specifically approved by a structural engineer.
- Choosing the type of board—whether structural as well as outdoor—is critical for project success.
*Jsylvl offers a comprehensive range of high-quality plywood products to meet diverse construction and manufacturing needs. The same goes for structural plywood boards, so it must be properly selected. - When subjected to high humidity, non-structural plywood with lower bond grades may fail, which emphasizes the importance of selecting the appropriate type of structural plywood.
In terms of longevity and durability, structural plywood, particularly with an A-bond, significantly outperforms non-structural varieties in demanding environments.
Understanding whether you require plywood is used to create structural components or for aesthetic purposes helps in selecting the appropriate type to use.
*Selecting the right plywood available involves balancing the structural needs with the environmental conditions and project budget to find it easier to achieve the best outcome.
Post time: Mar-11-2025