Plywood is a cornerstone of modern construction and manufacturing, prized for its strength, versatility, and cost-effectiveness. You've likely seen the standard 4 x 8 foot sheets on job sites or in building supply stores. But what makes this engineered wood product so essential? This article dives deep into the world of plywood, exploring different types like hardwood plywood, its role as structural-use panels, how it aligns with building code requirements, and understanding product standard classifications. Whether you're a construction company owner like Mark Thompson, a procurement officer, or a builder, understanding these details is crucial for ensuring project success, safety, and compliance. We'll cover everything from floor and roof sheathing to siding and underlayment, providing insights based on our experience as a specialized manufacturer.
1. What Exactly is Plywood and Why is 4x8 the Standard Size?
At its core, plywood is an engineered wood product made by gluing together thin layers of wood veneer. These layers, called plies, are typically oriented with their grain direction perpendicular to the adjacent layer. This cross-graining technique is what gives plywood its remarkable strength, stiffness, and resistance to warping or splitting compared to solid lumber. Think of it like weaving threads in fabric – the crisscross pattern creates a much stronger material.
The ubiquitous 4 x 8 foot (x 48 inches by x 96 inches) dimension isn't arbitrary. It emerged as a practical standard for several reasons:
- Compatibility with Framing: Standard construction framing often uses stud and joist spacing of 16 inches or 24 inches on center. A 4 x 8 sheet neatly covers multiple framing members, minimizing waste and cutting.
- Handling and Transport: While substantial, a 4 x 8 sheet is generally manageable for two workers to handle and fits efficiently onto trucks and into shipping containers.
- Manufacturing Efficiency: Producing large, consistent sheets is efficient with modern manufacturing processes.
This standard size simplifies design, estimation, and installation across countless applications, making the 4 x 8 plywood panel a fundamental unit in construction.
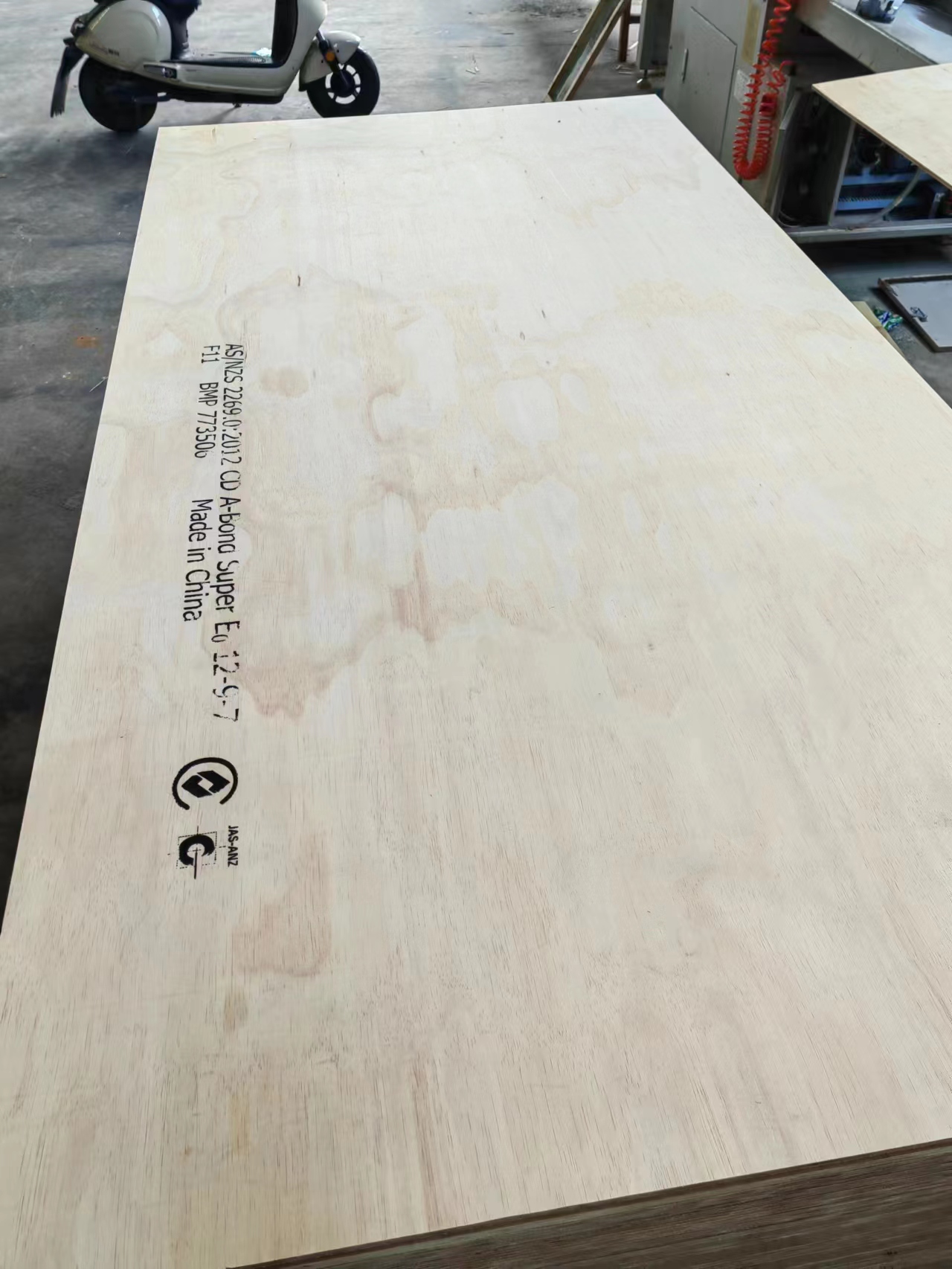
2. Decoding Plywood Grades: Structural vs. Non-Structural Uses?
Not all plywood is created equal! Panels are graded based on the quality of the face and back veneer layers and the type of adhesive used. Understanding these grades is critical for selecting the right panel for the job, especially for procurement officers needing reliable materials. A common grading system uses letters (A, B, C, D), where 'A' represents the highest quality veneer (smooth, paintable, few repairs) and 'D' allows for larger knots and defects.
The most crucial distinction, however, is often between structural and non-structural plywood:
- Structural Plywood: Designed and manufactured to meet specific strength and stiffness requirements outlined in building code and product standard specifications (like PS 1 or PS 2). These panels use exterior-grade adhesives and are intended for load-bearing applications such as roof sheathing, wall sheathing, subfloor, and diaphragm construction. They shall be marked with span ratings and structural classifications (e.g., STRUCTURAL I). Jsylvl offers a range of structural ply options suitable for demanding applications.
- Non-Structural Plywood: Often referred to as decorative or utility plywood, these panels prioritize appearance or cost over certified structural performance. They might use interior-grade adhesives and have lower quality cores or veneers. While useful for cabinets, furniture, temporary structures, or general utility purposes, they should not be used to resist structural loads where building code mandates rated panels. Check out our non-structural plywood for projects where aesthetics or basic coverage is key.
Choosing the correct grade ensures safety, longevity, and compliance with regulations. Using non-structural plywood where structural panels are required can lead to failure and liability.
3. Understanding Hardwood Plywood vs. Softwood Plywood?
The terms "hardwood" and "softwood" refer to the type of tree the veneer comes from, not necessarily the wood's actual hardness. Hardwood plywood uses veneers from deciduous trees (like oak, birch, maple), while softwood plywood uses veneers from coniferous trees (like pine, fir, spruce).
- Softwood Plywood: This is the most common type used in construction for structural applications like sheathing, subfloor, and framing components. It offers excellent strength-to-weight ratio and is generally more cost-effective. The grading system (A-D) typically applies here.
- Hardwood Plywood: Primarily valued for its appearance, hardwood plywood features a face veneer of attractive hardwood. It's commonly used for cabinets, furniture, wall paneling, and decorative elements. While the core layers might be softwood or other materials (composite core, particleboard core), the face provides the desired aesthetic. It often has different grading standards focused on the visual quality of the face veneer.
While hardwood plywood can possess structural properties if manufactured accordingly (using appropriate core veneers and exterior adhesives), its primary use is often aesthetic. Most structural plywood found in applications like floor and roof sheathing is softwood-based. When sourcing, it's vital to specify whether you need the structural capacity of softwood plywood or the aesthetic appeal of hardwood plywood.
4. How Does Plywood Fit into Building Codes and Product Standards?
Building code requirements are paramount in construction to ensure safety and structural integrity. Plywood used in structural applications must conform to specific performance levels defined by recognized product standard documents. In the United States, the primary standards are:
- PS 1: Structural Plywood
- PS 2: Performance Standard for Wood-Based Structural-Use Panels (includes plywood and OSB)
These standards, often referenced directly in the building code (like the International Building Code - IBC), set forth minimum requirements for wood species, veneer quality, adhesive type and durability, panel construction, dimensional tolerances, marking, and quality control. Panels that shall conform to these standards undergo rigorous testing and inspection.
For procurement officers like Mark Thompson, verifying that plywood meets the required product standard is crucial. Reputable manufacturers like Jsylvl ensure their structural plywood products are manufactured in accordance with these applicable standards. The presence of a grade stamp from a recognized third-party inspection agency (like the APA - The Engineered Wood Association, formerly American Plywood Association) provides assurance that the panels shall comply with the stated standard. Using non-compliant plywood can result in failed inspections, project delays, and potential structural issues.
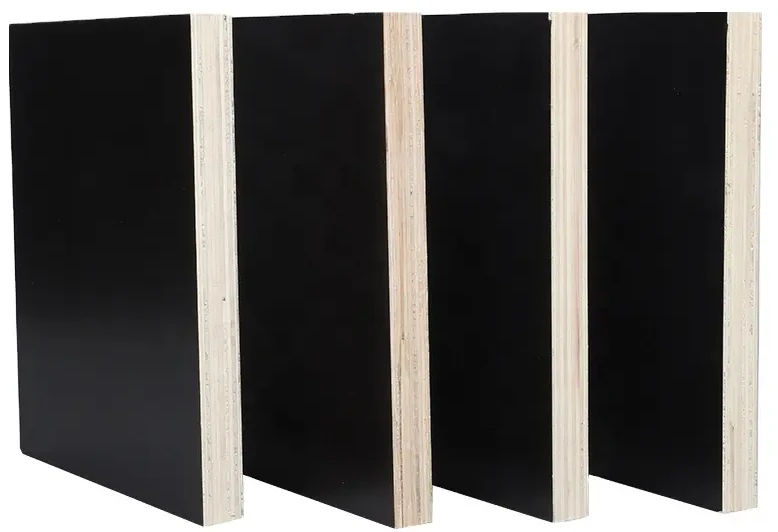
5. What are Structural-Use Panels and How is Plywood Classified?
The term "structural-use panels" is a broader category defined in standards like PS 2. It encompasses wood-based sheet materials designed and manufactured for structural applications in construction. This category includes:
- Plywood: Made from layers of wood veneer.
- Oriented Strand Board (OSB): Made from compressed strands or flakes of wood oriented in specific directions.
- Composite Panels: Panels combining veneer with other wood fiber materials.
Plywood within this classification is specifically engineered and tested to meet performance criteria for strength, stiffness, and bond durability under various environmental conditions. It's rated for specific end-uses like wall sheathing, roof sheathing, subfloor, and structural elements like shear walls and diaphragms.
Classification often involves:
- Span Rating: Indicates the maximum recommended center-to-center spacing of supports (joists or rafters) over which the panel can be installed. E.g., "32/16" means it can span 32 inches for roof sheathing and 16 inches for subfloor under standard loads.
- Exposure Durability: Classifies the panel's resistance to moisture during construction and its service life (Exterior, Exposure 1, Exposure 2, Interior). Structural plywood typically requires Exterior or Exposure 1 bond durability.
- Structural Grade: Such as STRUCTURAL I, which indicates enhanced shear capacity, often required for demanding diaphragm designs or permanent wood foundation systems.
Understanding that plywood is a key type of structural-use panels helps clarify its role in engineered construction systems.
6. Plywood for Flooring: Subfloor and Underlayment Explained
Plywood plays a critical role in floor systems, serving two main functions: subfloor and underlayment.
- Subfloor: This is the structural layer of the floor, installed directly over the floor joists. It provides the primary support for floor loads (furniture, people) and acts as a working platform during construction. Plywood used as subfloor must be structurally rated (conforming to PS 1 or PS 2) with an appropriate span rating for the joist spacing (e.g., 16 inches o.c., 24 inches o.c.). The panels shall be placed with the face grain perpendicular to the joists for maximum strength and stiffness. Proper installation, including edge support (tongue-and-groove edges or blocking) and correct fastening, is crucial. A common thickness is 3/4 inch (23/32").
- Underlayment: This is a thinner layer installed over the subfloor to create a smooth, uniform surface for the final floor covering (like vinyl, tile, or carpet). While it adds some stiffness, its primary role isn't structural load-bearing in the same way as the subfloor. Plywood underlayment grades (often marked "UNDERLAYMENT") have a smooth, sanded face (C-C Plugged & Touched Sanded is common) to prevent texture transfer. It's typically 1/4" to 1/2" thick. Particleboard or specialized underlayment panels may be used in lieu of plywood in some cases, depending on the finish floor requirements.
Using the correct type and thickness of plywood for both subfloor and underlayment is essential for a stable, durable, and high-quality floor system. Single-layer floor panels (thicker combination subfloor-underlayment panels) are also available, designed for direct application of certain floor coverings.
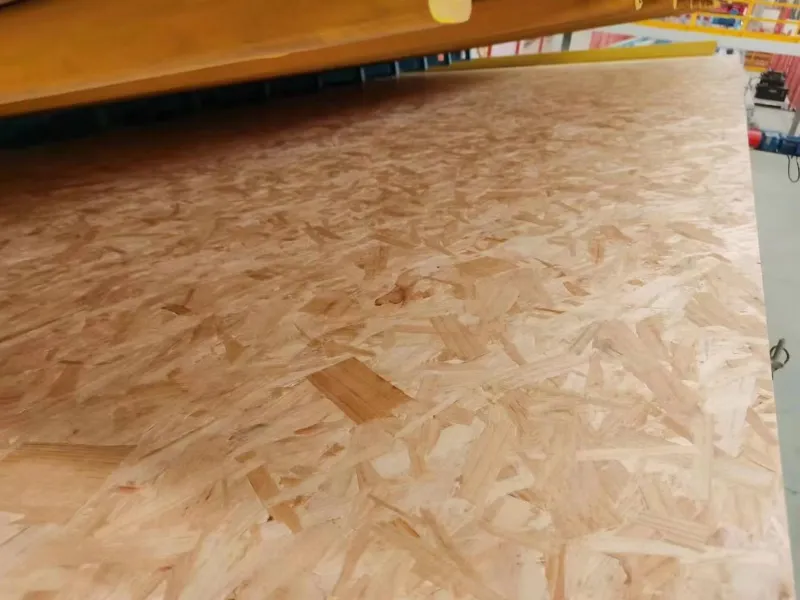
7. Plywood in Walls and Roofs: Sheathing and Shear Strength Considerations?
Plywood sheathing is fundamental to modern wall construction and roof assemblies, providing both structural integrity and a nailing base for exterior finishes.
- Wall Sheathing: Applied over wall studs, plywood wall sheathing braces the wall frame against lateral loads (like wind or seismic forces), significantly increasing its racking resistance or shear strength. It acts as a crucial component of the building's diaphragm system, transferring these loads down to the foundation. The required thickness and nailing pattern depend on the design loads and stud spacing. Panels can often be installed either horizontally or vertically. Proper nailing is critical to develop the full shear capacity.
- Roof Sheathing: Installed over rafters or trusses, plywood roof sheathing supports the roofing materials (shingles, tiles, membrane) and resists vertical loads (snow, dead load) and lateral loads (wind). Like subfloor, roof sheathing shall be installed with the face grain perpendicular to supports, typically spanning two or more spans for efficiency (roof sheathing continuous over two). The span rating marked on the panel dictates the maximum allowable rafter spacing for the given roof live load. Panel edges shall often require support using H-clips or blocking, especially for thinner panels or wider spacing.
In high-wind or seismic zones, plywood sheathing is integral to the design of shear walls and roof diaphragms. The plywood panels, combined with correct fastening and framing, create a strong, rigid plane capable of resisting and transferring significant lateral forces. The capacity of these diaphragms shall be designed based on factors like plywood thickness, nail size and spacing, and width of framing members. Consulting loading recommendations published by the American Plywood Association (APA) or engineered drawings is essential.
8. Can Plywood Be Used for Siding? What are the Specific Requirements?
Yes, plywood can be an excellent choice for exterior siding, offering both structural performance and a variety of aesthetic options. Plywood siding, often referred to as T1-11 (Texture 1-11) or panel siding, combines sheathing and siding into a single panel application.
Key considerations and specific requirements for plywood siding include:
- Grade and Type: Must be an exterior-rated plywood specifically manufactured and graded for siding use. It needs to withstand weather exposure. Look for panels marked "SIDING" or conforming to standards like PS 1 for siding.
- Texture and Appearance: Available in various surface textures (rough-sawn, brushed, grooved) and patterns (like vertical grooves simulating boards, e.g., 4 inches or 8 inches o.c.).
- Thickness: Typically 3/8", 1/2", or 5/8" thick. Thicker panels offer greater impact resistance and structural capacity. Sheathing shall be not less than the minimum required by code, even when combined siding/sheathing panels are used.
- Installation: Plywood siding applied directly to studs requires careful attention to fastening schedules, edge treatment (shiplapped or square edges needing caulking/flashing), and clearances from grade to prevent moisture wicking. Horizontal joints shall be backed with flashing. Panels shall be installed in accordance with manufacturer recommendations and building code requirements.
- Finishing: Proper priming and painting or staining are crucial for protecting the plywood siding from weathering and UV degradation, ensuring its longevity.
Using plywood siding can speed up construction by providing sheathing, shear resistance, and finish in one step. However, it demands careful installation and finishing details to perform correctly over the long term.
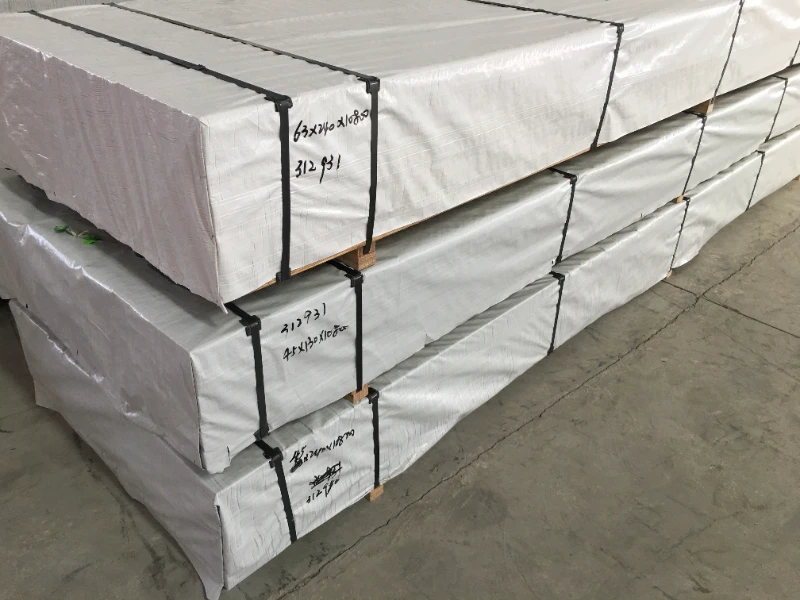
9. What are the Loading Recommendations for Plywood Sheathing?
Understanding loading recommendations is crucial for ensuring plywood sheathing performs safely under anticipated loads. These recommendations are typically based on extensive testing and inspection programs and are often published by organizations like the APA or included in engineering software. Key factors influencing load capacity include:
- Panel Thickness and Span Rating: Thicker panels or those with higher span ratings can generally support greater loads over wider spans.
- Support Spacing: The distance between joists, rafters, or studs (e.g., 16 inches, 24 inches). Loads shall be limited by the panel's capacity over the given span.
- Load Type and Duration: Recommendations consider different load types (uniform loads like snow, concentrated loads like a person walking) and durations (short-term like wind, long-term like stored materials).
- Deflection Limits: Loads are often based on deflection criteria (e.g., L/240 or L/360, where L is the span) to prevent excessive sagging, which can affect finish materials or occupant comfort. Maximum spans shown because of possible deflection issues under certain loads might be less than strength-based limits.
- Number of Spans: Panels continuous over two or more spans are generally stronger and stiffer than single-span panels.
- Fastening: The size, type, and spacing of fasteners significantly impact the panel's ability to transfer loads, especially shear loads in diaphragms.
Load tables (like shown in table X from APA guidelines) provide allowable uniform and concentrated loads for various plywood thicknesses, span ratings, and support spacings. It's critical that the design loads shall not exceed the values specified in these loading recommendations. For complex structures or high loads, a qualified engineer should determine the appropriate plywood specification and fastening schedule. As a supplier, we often help customers interpret these requirements to select the right structural panels.
10. Quality Control and Markings: What Should Buyers Like Mark Look For?
For buyers like Mark Thompson, ensuring consistent quality is a major concern. Reputable plywood manufacturers implement robust quality control procedures throughout the production process, from veneer peeling and drying to pressing and finishing. However, the grade stamp applied to the panel is the primary indicator of quality and compliance for the end-user.
Here's what buyers should look for on plywood markings (panels shall be marked):
- Panel Grade: Indicates the veneer quality (e.g., A-B, C-C, STRUCTURAL I).
- Span Rating: Shows suitability for subfloor and roof sheathing spans (e.g., 48/24).
- Exposure Durability Classification: (e.g., Exterior, Exposure 1). Essential for determining suitability for moisture conditions.
- Product Standard Conformance: Indicates compliance with standards like PS 1 or PS 2 (shall conform to the requirements).
- Thickness: The nominal thickness of the panel.
- Mill Number: Identifies the manufacturing facility.
- Third-Party Agency Logo: The mark of a recognized quality supervision agency (e.g., APA, TECO, PFS). This signifies that the manufacturer's quality control program is audited by an independent body. Testing and inspection by such agencies provide confidence in the product's performance.
Inspecting panels upon arrival for physical damage, consistent thickness, and clear, correct markings is also vital. Any discrepancies or missing information should be addressed with the supplier immediately. Verifying the authenticity of certifications is also key, sometimes requiring direct contact with the certifying agency, especially when sourcing from new suppliers. Consistent quality control and transparent marking are hallmarks of a reliable plywood supplier.
11. Handling and Storage: Best Practices for Plywood Panels?
Proper handling and storage are essential to maintain the quality and usability of plywood panels, preventing damage that could compromise performance or appearance. Here are some best practices we recommend:
- Keep Dry: Plywood should be protected from rain, snow, and ground moisture. Store panels under cover on a flat, level surface. Use supports (stickers or dunnage) to keep the stack elevated off the ground (at least 4-6 inches).
- Support Flat: Stack panels flat to prevent warping. Use enough supports spaced adequately (e.g., every 12 inches to 16 inches) to prevent sagging, especially for thinner panels or longer storage periods.
- Protect Edges and Corners: Edges and corners are most susceptible to damage during handling. Use care when moving panels, avoiding dropping or dragging them.
- Acclimatize (If Necessary): For interior applications requiring dimensional stability (like underlayment or cabinetry), allow plywood panels to acclimatize to the building's temperature and humidity for 48-72 hours before installation.
- Cover Stacks: If stored outdoors temporarily, cover the top and sides of the stack loosely with a protective material (like plastic sheeting) that allows air circulation to prevent condensation buildup.
- Use Proper Equipment: Use forklifts with appropriate forks or manual labor carefully to move stacks or individual sheets.
Following these simple steps helps ensure that the plywood you purchased arrives at the point of installation in optimal condition, ready to perform as intended, whether it's for sturdy floor systems, reliable wall sheathing, or beautiful hardwood finishes. This protects your investment and prevents costly delays or replacements due to damaged materials.
Key Takeaways:
- Plywood is a versatile engineered wood product made from cross-laminated veneers, commonly available in 4 x 8 sheets.
- Grades distinguish between structural panels (for load-bearing uses like sheathing and subfloor) and non-structural/decorative panels. Always use the correct grade per building code.
- Hardwood plywood is valued for appearance, while softwood plywood forms the backbone of structural applications.
- Structural plywood shall conform to product standard requirements (like PS 1 or PS 2) and shall be marked accordingly. Look for third-party certification stamps.
- Plywood serves critical roles in floor (subfloor, underlayment), wall (wall sheathing, shear walls), and roof (roof sheathing) systems, contributing to the building's diaphragm.
- Specialty plywood siding combines structure and finish but requires careful installation and finishing.
- Adhere to loading recommendations and span ratings marked on panels, considering loads, spans, and deflection limits. Correct fastening is vital.
- Verify quality control through clear markings and third-party certifications. Inspect panels upon receipt.
- Proper handling and storage (keeping dry, flat, and protected) are crucial to maintain plywood quality.
Understanding these aspects of plywood helps ensure you select and use the right materials for safe, compliant, and durable construction projects. As a manufacturer, we are committed to providing high-quality wood products, including various types of plywood, OSB board, and LVL Timber, meeting rigorous standards for customers worldwide.
Post time: Mar-28-2025