Choosing the right subfloor material is a critical decision in any construction project. Both oriented strand board (OSB) and plywood are popular choices, each with its own set of advantages and disadvantages. This article delves into the core differences between OSB and plywood, exploring their strengths, weaknesses, and ideal applications to help you make an informed decision for your next build. Understanding these nuances is crucial for builders and procurement officers alike, ensuring both quality and cost-effectiveness.
What are OSB and Plywood, and What Makes These Subfloor Materials Different?
Oriented strand board, or OSB, is an engineered wood product made from thin wood strands, also referred to as flakes, that are arranged in layers and then compressed together with adhesives. These strands, often around 50 layers of strands in thicker panels, are oriented in specific directions for added strength, hence the name. This process to make osb involves mixing the wood strands with resin and compressing them under high pressure and heat.
Plywood, on the other hand, is also an engineered wood product, but it consists of thin sheets of wood veneer, called plies, that are glued together with the wood grain of adjacent layers oriented at right angles to one another. This cross-graining gives plywood its characteristic strength and stability. Think of it like layers of solid wood stacked and bonded. Both materials are versatile building products, but their manufacturing processes and resulting properties differ significantly.
OSB Subflooring: What are the Pros and Cons of Using Oriented Strand Board for Floors?
OSB was introduced as a cost-effective alternative to plywood and has become a widely used subflooring material. One of the main pros of osb is its affordability. Generally, a sheet of osb is less than plywood, making it an attractive option for builders looking to manage costs. OSB also tends to be very consistent in its density and thickness throughout the panel, which can be beneficial for installation. Furthermore, OSB panels are typically large, which can mean faster coverage of floor areas.
However, there are also cons to consider. OSB is more prone to absorbing moisture compared to plywood. When exposed to moisture, osb tends to swell, which can lead to issues like uneven flooring and potential mold growth. This makes it crucial to keep OSB dry during construction. While advancements have improved OSB's water resistance, it generally doesn't perform as well as plywood in damp conditions. The durability of OSB can also be a concern in environments where it might be repeatedly exposed to moisture.
Plywood Subflooring: What are the Advantages and Disadvantages of Using Plywood for Subfloors?
Plywood is a time-tested and reliable material for subfloors. Plywood is strong and offers excellent structural integrity. Its cross-laminated construction makes it resistant to bending and warping, providing a stable base for the final floor covering. Another significant advantage of using plywood is its superior resistance to moisture compared to osb. While not entirely waterproof, plywood is less likely to swell or delaminate when briefly exposed to water. This makes plywood for flooring a popular choice in areas where moisture might be a concern during construction.
Despite its benefits, plywood also has some disadvantages. The primary con is cost; plywood is often more expensive than OSB. The price difference can be significant, especially for large projects. Also, the quality of plywood can vary depending on the grade plywood and the manufacturing process. Delamination can occur if the adhesive between the plies fails, although high-quality plywood is generally very reliable.
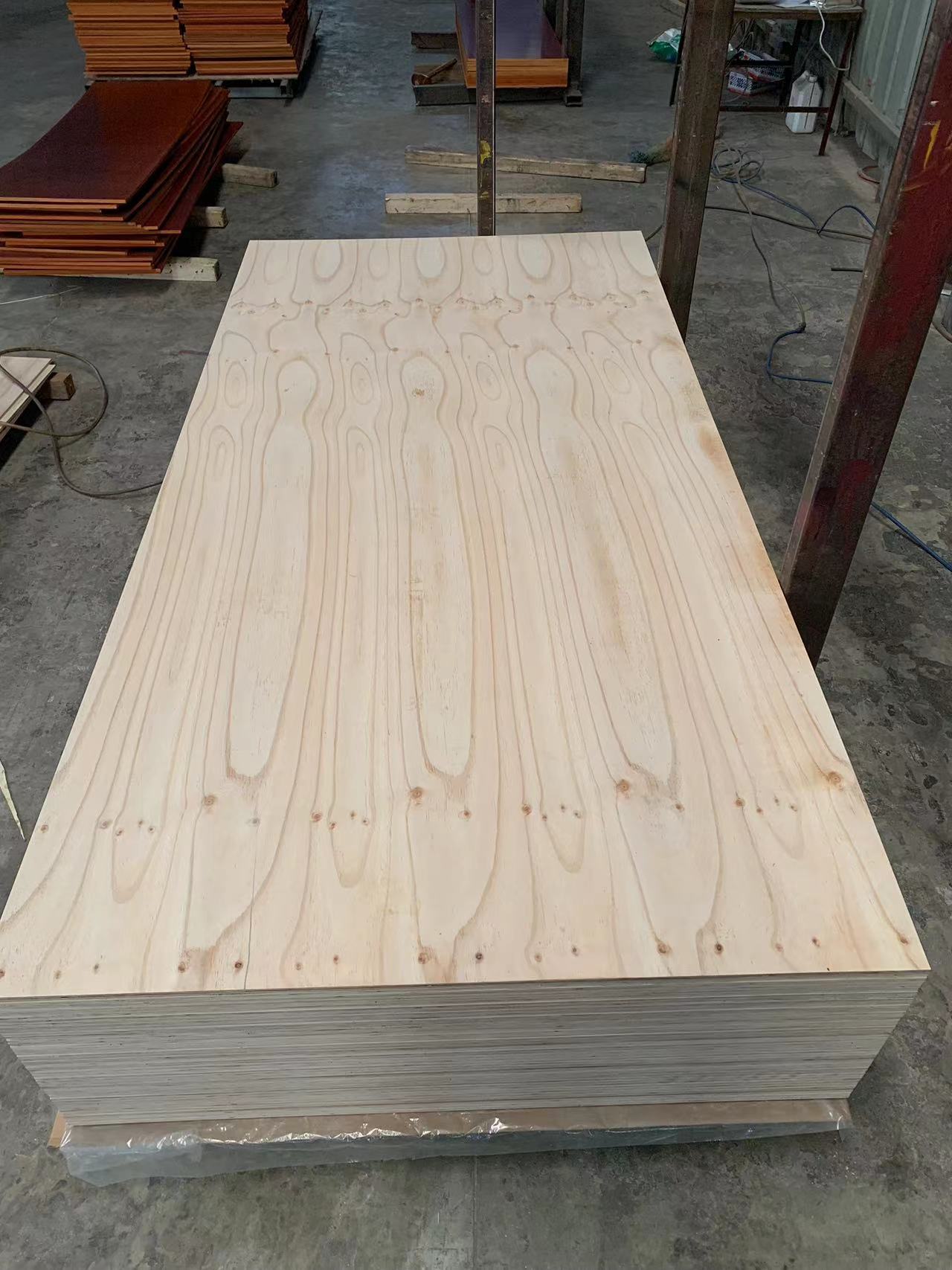
High-quality plywood ready for use.
Plywood vs. OSB Subfloor: When Comparing Strength, Which Material for Your Floor Wins?
When comparing the sheer strength of plywood vs osb, both materials perform well in many applications. However, the type of plywood and its grade can influence its strength characteristics. Structural grades of plywood are designed for demanding applications and offer excellent load-bearing capacity. Plywood is strong in all directions due to its cross-laminated structure.
OSB, while strong, has its strength primarily oriented along the direction of the wood strands. For subfloor applications, both materials, when installed correctly and meeting building codes, provide adequate strength. The choice often comes down to other factors like moisture resistance and cost. It's important to note that both plywood and oriented strand board are engineered wood products designed to offer predictable performance when used according to specifications.
How Does OSB React to Water and Moisture Compared to Plywood Subflooring?
The reaction of OSB and plywood to water is a key differentiator. OSB is more susceptible to moisture damage. When OSB absorbs water, the wood strands can swell considerably, leading to thickness increases and potentially an uneven surface. Prolonged exposure to moisture can cause delamination and reduce the structural integrity of the osb subfloor.
Plywood, with its layers of veneer bonded together, offers better resistance to swelling and delamination when exposed to moisture. While prolonged soaking will damage any wood product, plywood can withstand incidental moisture exposure better than OSB. This difference is critical in areas where construction might be exposed to rain or in environments with higher humidity. For Mark Thompson in the USA, where varying climates exist, understanding this difference is paramount.
For Subfloors, is Plywood or OSB the Better Option in Areas with High Potential for Moisture?
In areas where moisture is a significant concern, plywood is generally the better option for subfloors. Bathrooms, kitchens, and basements, or regions with consistently high humidity, benefit from plywood's superior moisture resistance. While proper sealing and ventilation are essential regardless of the material used, plywood offers an extra layer of protection against moisture-related issues like swelling, warping, and mold growth.
Using plywood in these areas can help prevent costly repairs and maintain the integrity of the flooring system over time. If you anticipate that the subfloor might be exposed to moisture during construction or in its final environment, investing in plywood can be a wise decision. For instance, coastal regions or areas with frequent rainfall would be locations where plywood may be preferred over osb for subflooring.
What are the Cost Differences Between OSB and Plywood Subfloor Material per Square Foot?
Cost is a significant factor for many builders, and this is where OSB often has an advantage. Generally, the cost per square foot of OSB is less than plywood. This price difference can be substantial, especially on large-scale projects. The savings can be attractive, but it's important to weigh the initial cost savings against potential long-term costs associated with moisture damage or reduced durability, particularly in damp environments.
While OSB offers a lower upfront cost, consider the overall value and the potential need for repairs or replacements down the line if moisture becomes an issue. For budget-conscious projects in dry climates, OSB can be a viable option, but in areas prone to moisture, the higher initial investment in plywood may prove more economical in the long run.
OSB or Plywood for Subfloors: What Do Building Codes and Engineers Typically Recommend?
Building codes often allow for the use of both OSB and plywood for subfloors, provided they meet specific performance standards and thickness requirements. Check your local building codes to ensure compliance. Engineers typically consider the specific demands of the project, including load requirements and potential moisture exposure, when making recommendations.
While both materials can meet code requirements, engineers might lean towards plywood in situations where structural integrity and moisture resistance are paramount. It's always best to consult with a structural engineer or local building officials to determine the most appropriate subflooring material for your specific project. They can provide guidance based on your region's climate and the building's design.
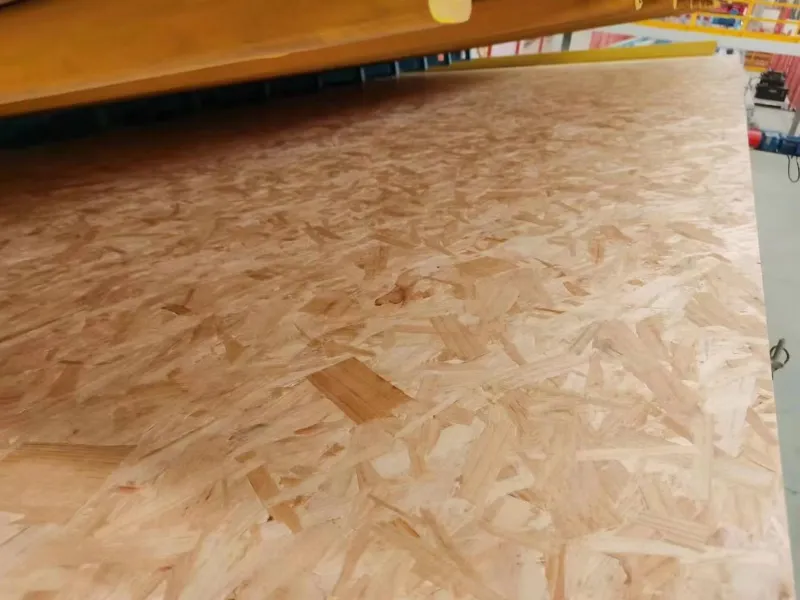
Large OSB panels for efficient floor coverage.
Beyond Subflooring: Where Else Are OSB and Plywood Commonly Used as Sheathe and Other Building Materials?
Both OSB and plywood have a wide range of applications beyond subflooring. They are commonly used for wall sheathing and roof sheathing, providing structural support and a nailing surface for siding and roofing materials. Plywood is often favored for applications requiring higher strength and moisture resistance, such as exterior siding or concrete formwork. Our Formply F17 is an excellent example of plywood designed for concrete forms, offering durability and a smooth surface.
OSB is also widely used for sheathing and in other structural applications where cost-effectiveness is a primary concern. Additionally, both materials find their way into various manufactured products, from furniture components to packaging. The versatility of both OSB and plywood makes them essential materials in the building construction industry. For door manufacturers, our LVL For Doors provides a stable and reliable core material, showcasing another key application of engineered wood.
Making the Right Choice: How to Decide Between OSB and Plywood for Your Specific Subfloor Needs?
Choosing between OSB and plywood for your subfloor involves considering several factors. Evaluate the potential for moisture exposure in your project's location and within the building itself. If moisture is a significant concern, plywood is likely the better choice. Consider your budget; OSB offers a lower initial cost, but factor in potential long-term costs related to moisture damage.
Assess the structural requirements of your project. Both materials are suitable for most residential subfloor applications when installed correctly, but for demanding structural loads, high-grade plywood may be preferable. Finally, consult local building codes and consider the recommendations of engineers or experienced builders. By carefully weighing these factors, you can make an informed decision that balances cost, performance, and durability for your subfloor. Remember, a strong foundation starts with the right materials. For structural applications demanding high performance, consider our range of Structural Plywood.
Key Takeaways:
- OSB is generally more affordable but more susceptible to moisture damage compared to plywood.
- Plywood offers superior moisture resistance and strength but comes at a higher cost.
- Consider the environment: Plywood is better suited for areas with high moisture potential.
- Check local building codes for specific requirements and recommendations.
- Both OSB and plywood are versatile materials with applications beyond subflooring, such as wall and roof sheathing.
- The right choice depends on a balance of cost, performance needs, and environmental factors.
- For reliable structural performance, especially where moisture is a concern, plywood is often the preferred material.
- OSB can be a cost-effective solution in dry environments.
- Always ensure proper installation and sealing regardless of the material chosen.
- Consult with professionals for project-specific advice.
By understanding the nuances of OSB and plywood, you can make an informed decision that contributes to the long-term success and durability of your building projects. For more information on engineered wood products, visit our website to explore our range of LVL Timber and other high-quality building materials. We offer a variety of options to meet your specific construction needs.
Post time: Jan-21-2025