Plywood is a versatile and widely used building material in construction, furniture making, and various other applications. However, one common challenge faced by builders and suppliers alike is plywood warping. This deformation can compromise the structural integrity and aesthetic appeal of finished projects. This article provides a comprehensive guide on how to prevent plywood from warping, drawing on the expertise of a seasoned professional in the engineered wood products industry. Reading this article will equip you with practical knowledge, tips, and techniques to ensure your plywood remains flat and stable, saving you time, money, and frustration in the long run.
1. What is Plywood Warping and Why Does it Matter?
Plywood warping refers to the unwanted bending or deformation of plywood sheets. It can manifest as a twist, cup, bow, or a combination of these. Instead of lying flat, the plywood develops a curvature, making it difficult to use in construction or furniture making.
Warping matters significantly because it affects both the structural integrity and the visual appeal of projects. Warped plywood can lead to uneven surfaces, weakened joints, and difficulty in achieving precise fits. This, in turn, can lead to costly rework, material waste, and potential safety hazards. In the B2B realm, supplying warped plywood can damage a supplier's reputation and lead to loss of business.
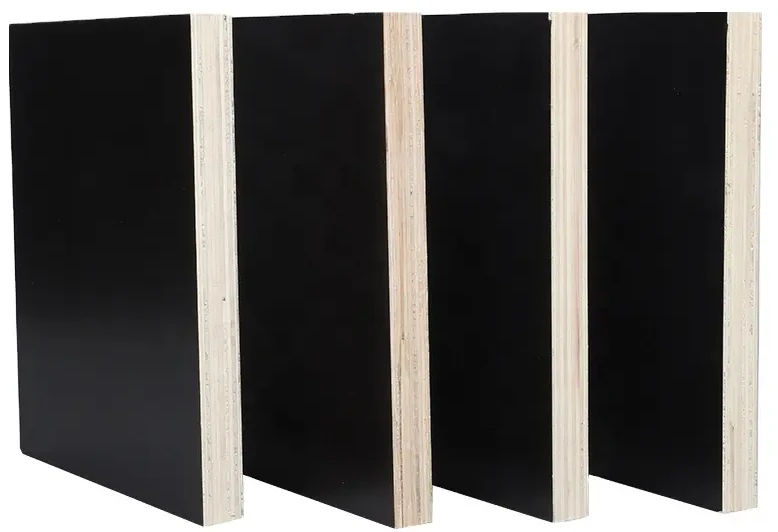
2. Understanding the Causes of Plywood Warping: What Makes Plywood Bend?
Plywood, being a wood-based product, is inherently susceptible to changes in its environment. There are three major interconnected factors that contribute to plywood warping: moisture, temperature, and external forces. Fundamentally, plywood warping arises from internal stress within the plywood.
Internal stress is induced mainly due to the uneven expansion or contraction. This is because the plywood’s construction by design, is a layered composite. These layers, called veneers, can react differently to changes. The wood fibers within each veneer try to expand or contract, but the adhesive and the arrangement of layers might restrain them. This leads to stresses building up inside the plywood sheet.
3. How Does Moisture Content Affect Plywood Stability?
Plywood is a hygroscopic material, meaning it readily absorbs and releases moisture from the surrounding air. Changes in moisture content are the primary cause of plywood warping. When plywood absorbs moisture, the wood fibers swell; when it dries, they shrink. Uneven moisture absorption or evaporation across the plywood sheet leads to differential expansion and contraction, causing it to bend.
Maintaining a consistent moisture content within the plywood is crucial. The ideal moisture content for plywood typically ranges from 6% to 14%, depending on the wood species and the intended application. Significant deviations from this range, especially sudden or uneven changes, will almost certainly lead to warping. For instance, 12mm Film faced plywood needs careful handling to prevent moisture related issues.
4. Can Temperature Fluctuations Cause Plywood to Warp?
Yes, temperature fluctuations can certainly cause plywood to warp. While moisture content is the primary driver, temperature changes exacerbate the issue. Heat causes wood to expand, while cold causes it to contract.
When plywood is subjected to significant temperature changes, especially rapid ones, it can amplify the effects of moisture-related expansion and contraction. For example, leaving plywood sheets in direct sunlight on a hot day can cause the exposed surface to dry and shrink much faster than the shaded side, leading to warping. The same principle applies to cold weather, where the rapid temperature changes can create uneven stress distribution, causing the plywood to bend.
5. Is Improper Storage a Major Factor in Plywood Deformation?
Absolutely. Improper storage is a very significant factor in plywood deformation. Storing plywood incorrectly exposes it to uneven moisture absorption, temperature variations, and physical pressure, all of which contribute to warping.
For example, storing plywood sheets directly on a concrete floor allows moisture from the floor to be absorbed into the bottom sheet, causing it to expand more than the top sheet. Similarly, leaning plywood sheets against a wall creates uneven pressure and airflow, leading to bowing. Stacking plywood of different sizes without proper support can also cause uneven loading and warping.
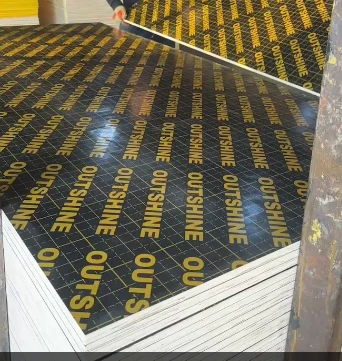
6. The Role of Manufacturing Processes in Preventing Plywood Warping
The manufacturing process plays a critical role in the inherent stability of plywood. High-quality plywood, like that produced by a reputable factory with multiple production lines, undergoes several steps designed to minimize warping.
- Veneer Drying: Ensuring that the veneers are dried to a uniform and appropriate moisture content before gluing is essential.
- Glue Application: Using the correct type and amount of adhesive, and applying it evenly, ensures a strong and consistent bond between the veneers.
- Pressing: Applying uniform pressure and temperature during the pressing process is vital for creating a stable and flat plywood sheet.
- Quality Control: Rigorous quality checks throughout the manufacturing process, including monitoring moisture content, veneer thickness, and glue spread, help identify and correct any potential issues before the plywood leaves the factory.
7. How to Choose the Right Type of Plywood to Minimize Warping
Selecting the appropriate type of plywood for a specific application is crucial in minimizing the risk of warping. Different types of plywood have varying degrees of resistance to moisture and temperature changes.
- Structural Plywood: Designed for applications where strength and stability are paramount, such as subfloors and roofing. It's typically made with a higher grade of adhesive and is more resistant to moisture. structural ply offers good stability.
- Non-Structural Plywood: Suitable for interior applications where exposure to moisture is minimal, such as wall paneling and furniture.
- Marine Plywood: Manufactured with waterproof glue and high-quality veneers, making it highly resistant to moisture and suitable for use in boats and other marine environments.
- Film-Faced Plywood: Coated with a resin-impregnated film, providing a durable and water-resistant surface. Often used in concrete formwork. Formply F17 1800×1200×17mm is a good example of this type.
- OSB (Oriented Strand Board): Made from wood strands oriented in specific directions and bonded with resin, OSB can offer good dimensional stability, although it's generally more susceptible to moisture than plywood.
Consider these factors when selecting plywood:
Plywood Type | Moisture Resistance | Warping Resistance | Typical Uses |
---|---|---|---|
Structural Plywood | High | High | Subfloors, roofing, sheathing |
Non-Structural Plywood | Low | Low | Interior paneling, furniture |
Marine Plywood | Very High | Very High | Boats, marine applications |
Film-Faced Plywood | High | High | Concrete formwork, exterior applications |
OSB Board | Medium | Medium | Sheathing, subfloors, some structural uses |
8. Best Practices for Storing Plywood to Maintain its Flatness
Proper storage is paramount to preventing plywood warping. Here are some best practices:
- Store Flat: Always store plywood sheets horizontally on a flat, level, and dry surface. Use supports (stickers) of uniform thickness placed at regular intervals (e.g., every 16 inches) to prevent sagging.
- Keep Dry: Protect plywood from direct contact with water and moisture. Store it in a well-ventilated area with low humidity. A climate-controlled environment is ideal.
- Cover Plywood: Use a waterproof cover to protect the plywood from dust, debris, and moisture, but ensure there's still adequate ventilation to prevent condensation buildup.
- Avoid Direct Sunlight: Prolonged exposure to direct sunlight can cause uneven drying and warping.
- Acclimatize: Allow plywood to acclimatize to the environment where it will be used for at least 24-48 hours before installation. This helps equalize the moisture content and reduce the risk of warping after installation.
- Stack Evenly: If stacking multiple sheets, ensure they are of the same size and thickness. Place heavier sheets at the bottom.
9. Effective Techniques for Handling and Installing Plywood to Prevent Warping
Even with proper storage, improper handling and installation can induce warping. Follow these guidelines:
- Support During Transport: When transporting plywood, ensure it's fully supported to prevent bending or flexing. Use a flatbed truck or trailer and secure the sheets properly.
- Avoid Dropping or Banging: Handle plywood sheets carefully to avoid damaging the edges or corners, which can weaken the structure and make it more susceptible to warping.
- Use Proper Fasteners: When installing plywood, use the correct type and size of fasteners (screws or nails) and space them appropriately. Over-driving fasteners can create stress points.
- Allow for Expansion and Contraction: Leave a small gap (e.g., 1/8 inch) between plywood sheets to accommodate expansion and contraction due to changes in humidity and temperature. This is especially important for flooring and roofing applications.
- Correct Orientation: When constructing with plywood, pay attention to the orientation of the veneers. For maximum strength and stability, alternate the direction of the grain in adjacent layers. Generally, the face grain should run perpendicular to the supports.
10. Can You Flatten Warped Plywood? Methods and Limitations
While preventing warping is always the best approach, sometimes you may encounter warped plywood. Flattening warped plywood can be attempted, but the success rate varies depending on the severity of the warp and the type of plywood. Here are a couple of methods:
- Moisture and Weight Method: For minor warping, lightly mist the concave side of the plywood with water. Place the plywood on a flat surface with the concave side facing up. Apply even weight across the entire surface (e.g., using heavy books or concrete blocks). Allow the plywood to dry slowly under the weight. This method works best for thinner plywood sheets.
- Clamping and Drying: For more significant warping, you can try clamping the plywood to a flat, rigid surface (like a workbench or a heavy table). Gradually tighten the clamps, applying even pressure to flatten the plywood. You may need to combine this with the moisture method, applying moisture to the concave side.
Limitations:
- These methods are not always effective, especially for severely warped plywood or plywood made with lower-quality materials.
- Over-wetting the plywood can cause further damage, such as delamination (separation of the layers).
- Even if successful, the plywood may still be weaker than it was originally and more prone to warping again in the future.
- It is often used for a structural purpose, you should not manipulate it and just change for a new one. The defect can have been costly, but it is not worth the risk.
11. The Importance of Quality Control and Certifications in Avoiding Warped Plywood
When purchasing plywood, especially in a B2B context, paying close attention to quality control and certifications is crucial for avoiding warped material. Reputable suppliers, particularly factories with multiple production lines like Jsylvl, implement rigorous quality control measures throughout their manufacturing process.
Key Certifications to Look For:
- FSC (Forest Stewardship Council): Ensures that the wood comes from responsibly managed forests. While not directly related to warping, it indicates a commitment to sustainable practices.
- CARB (California Air Resources Board): Regulates formaldehyde emissions in composite wood products. Low formaldehyde emissions are important for indoor air quality.
- Structural Certifications (e.g., APA – The Engineered Wood Association): These certifications indicate that the plywood meets specific performance standards for structural applications.
Quality Inspection Points:
- Grade: Check the plywood grade to ensure it's appropriate for the intended use. Higher grades typically have fewer defects and better resistance to warping.
- Moisture Content: Verify that the moisture content is within the acceptable range (typically 6-14%).
- Lamination Quality: Inspect the edges of the plywood for any signs of delamination or gaps between the veneers.
- Dimensional Accuracy: Measure the thickness, length, and width of the plywood sheets to ensure they meet the specified dimensions.
"As a procurement officer, I always prioritize suppliers who can provide detailed quality reports and certifications," says Mark Thompson, a US-based company owner. "It's not just about the price; it's about ensuring the long-term performance and reliability of the materials we use in our projects."
Summary: Key Takeaways for Preventing Plywood Warping
- Moisture is the Enemy: The primary cause of plywood warping is uneven moisture absorption and evaporation.
- Store Flat and Dry: Proper storage is crucial. Store plywood horizontally on a flat, dry surface, protected from moisture and temperature extremes.
- Choose the Right Plywood: Select the appropriate type of plywood for your application, considering factors like moisture resistance and structural requirements.
- Handle with Care: Avoid dropping, banging, or bending plywood during transport and installation.
- Acclimatize: Allow plywood to acclimatize to the environment before installation.
- Allow for Expansion: Leave small gaps between sheets to accommodate expansion and contraction.
- Prioritize Quality: Purchase plywood from reputable suppliers who adhere to strict quality control standards and provide relevant certifications.
- Regular Inspection: Conduct regular inspections of your plywood inventory to identify and address any potential warping issues early on.
- Temperature Control: Avoid extreme temperature changes and direct sunlight exposure, both during storage and after installation.
By understanding the causes of plywood warping and taking proactive preventive measures, you can significantly reduce the risk of encountering this problem, ensuring the success and longevity of your projects. Remember, investing in high-quality plywood and implementing proper storage and handling techniques is always more cost-effective than dealing with the consequences of warped plywood.
Post time: Mar-25-2025