Looking for a reliable and cost-effective solution for your concrete formwork or high-wear applications? Dive into our comprehensive guide on film faced plywood and formply. We'll explore everything from its waterproof properties and durability to its diverse applications in construction and beyond. Discover why film faced plywood is becoming an increasingly popular choice for builders and manufacturers worldwide.
1. What is Film Faced Plywood and Why is it Called Formply? Understanding the Basics of Film Faced Ply and Formply
Film faced plywood, often referred to as formply, is a specialized type of plywood distinguished by its outer coating of a film face. This isn't just any film; it's usually a phenolic film or melamine-impregnated paper applied to both sides of the plywood sheets. This film coating is what gives film faced plywood its unique properties and makes it a popular choice in various industries, most notably in concrete formwork.
But why "formply"? The name "formply" is derived directly from its primary application: creating forms for pouring concrete. In the concrete formwork industry where certified plywood is not required, formply acts as the mold that shapes and contains wet concrete until it sets and hardens. The smooth, film-faced surface of the formply sheets ensures a smooth finish on the concrete form, reducing the need for extensive post-casting work. Think of it as the unsung hero behind every smooth concrete wall, pillar, or foundation you see. Its robust nature allows it to withstand the pressure of wet concrete, making it indispensable on construction sites around the globe.
2. Film Faced Plywood vs. Regular Plywood: Key Differences You Need to Know - Comparing Film Face Ply with Standard Plywood Options
When comparing film faced plywood to regular plywood, the differences are significant and directly impact their suitability for various applications. Regular plywood, often used for general construction, furniture, and joinery, is typically made from wood veneers glued together, but lacks the protective film coating. This makes plywood is non-structural rated plywood and also more susceptible to wear and tear, moisture, and surface damage compared to its film-faced counterpart.
Here’s a table summarizing the key distinctions:
Feature | Film Faced Plywood (Formply) | Regular Plywood |
---|---|---|
Surface | Smooth, film-coated (phenolic/melamine) | Wood veneer surface, often rougher |
Water Resistance | Waterproof, highly water-resistant | Less water-resistant, susceptible to moisture damage |
Durability | High, resistant to abrasion and chemicals | Moderate, less resistant to damage |
Reusability | Can be reused multiple times in formwork (formply: 1-19 times) | Limited reusability, especially in wet conditions |
Finish on Concrete | Smooth finish | Rougher finish on concrete |
Applications | Concrete formwork, high-wear surfaces, transport, furniture where moisture is a concern | General construction, furniture, joinery, interior applications |
Cost | Generally more expensive initially, but cost-effective due to reusability and durability | Generally less expensive upfront |
As you can see, while regular plywood serves many purposes well, film faced plywood is engineered for demanding applications requiring superior durability and waterproof qualities. For projects where longevity and resistance to harsh conditions are paramount, film faced ply is the clear winner.
3. What Makes Film Faced Plywood Waterproof and Ideal for Concrete Formwork? - Exploring the Waterproof Nature of Film Faced Plywood
The waterproof nature of film faced plywood, which is crucial for its effectiveness in concrete formwork, stems from several key factors. Firstly, the phenolic film or melamine facing itself is inherently water-resistant. This film acts as a barrier, preventing water and moisture from penetrating the underlying wood veneer. Think of it like a raincoat for the surface of the plywood.
Secondly, the manufacturing process plays a vital role. High-quality film faced plywood uses phenolic resin adhesives to bond the layers of wood veneers glued together. Phenolic resins are known for their excellent waterproof properties and create a strong, moisture-resistant bond throughout the plywood sheets. This combination of a water-resistant surface film and waterproof adhesive ensures that film faced plywood can withstand prolonged exposure to wet concrete, rain, and humidity without delamination or significant water absorption. This waterproof plywood characteristic is not just beneficial for formwork; it also makes film faced plywood suitable for outdoor applications where exposure to the elements is unavoidable.
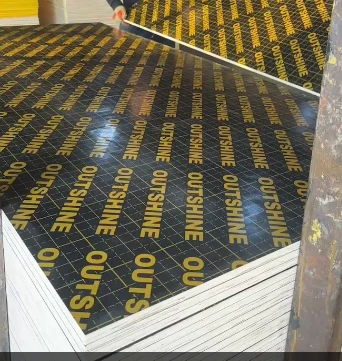
Phenolic film faced plywood, known for its waterproof qualities.
4. Formply Demystified: Is Formply Just Another Name for Film Faced Plywood? - Clarifying the Terminology: Formply vs. Film Faced Plywood
The terms "formply" and "film faced plywood" are often used interchangeably, and for good reason: they essentially refer to the same product in many contexts. However, the term "formply" is more application-specific, highlighting its primary use in concrete formwork. Essentially, all formply is film faced plywood, but not all film faced plywood is necessarily used as formply.
You can think of it this way: film faced plywood is the broader category, describing any plywood with a film coating. Formply is a subset within this category, specifically manufactured and marketed for concrete formwork applications. Therefore, when you hear "formply," you can confidently assume it's film faced plywood designed to withstand the pressure and moisture of concrete form. While technically interchangeable in many discussions, "formply" emphasizes the intended use, while "film faced plywood" describes the product's construction.
5. The Impressive Durability of Film Faced Plywood: How Many Times Can Formply Be Reused? - Assessing the Lifespan and Reusability of Formply
One of the most significant advantages of formply (film faced plywood) is its exceptional durability and reusability, especially when compared to traditional timber formwork or regular plywood. High-quality formply can withstand multiple uses in concrete formwork, significantly reducing material costs and waste over time.
The number of reuses depends on several factors, including the quality of the formply, the thickness of the film coating, handling practices on site, and the complexity of the concrete pours. Generally, formply made with a hardwood or birch core plywood and a thick phenolic film can be reused 16-40 times if handled carefully. Lower grades or those with thinner film faces might offer fewer reuses, perhaps in the range of 1-19 times. This reusability makes formply a cost-effective and environmentally responsible choice for large construction projects. Imagine the savings in material costs and labor over a multi-story building project simply by reusing your formply sheets multiple times!
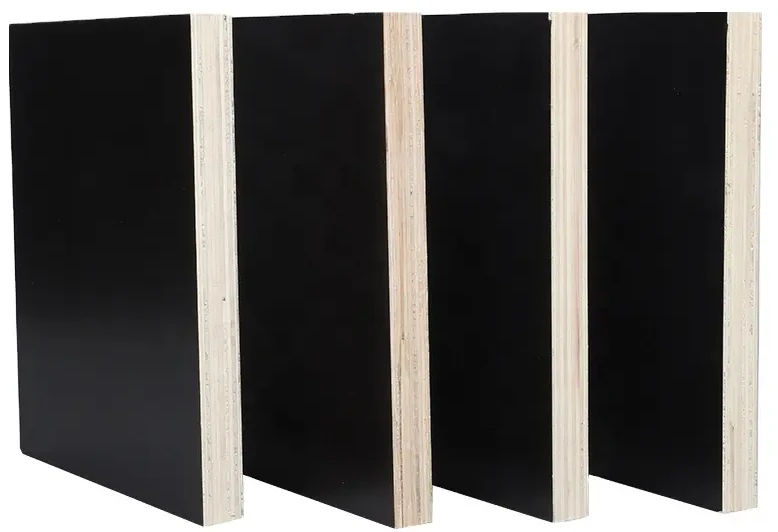
Film faced plywood used in concrete formwork applications.
6. What are the Different Applications of Film Faced Plywood Beyond Concrete Formwork? - Discovering Versatile Uses of Film Faced Plywood in Construction and Joinery
While concrete formwork is the most well-known application for film faced plywood (formply), its unique properties make it incredibly versatile for a wide range of other uses. Its strength and durability, combined with its smooth finish and waterproof nature, open doors to numerous applications in construction, transport, furniture, and more.
Beyond formwork, film faced plywood is excellent for:
- Flooring in high-wear areas: Warehouses, factories, and transport vehicles benefit from its robust surface. Consider using it for a durable, easy-to-clean floor in a commercial space.
- Scaffolding and work platforms: Its load-bearing capacity and weather resistance make it safe and reliable for temporary structures. Our LVL scaffold planks utilize similar principles for enhanced safety and strength.
- Vehicle building: Truck and trailer beds, as well as internal linings, take advantage of its durability and resistance to wear and tear.
- Furniture and joinery: For projects requiring water-resistant and easy-to-clean surfaces, such as kitchen cabinets, bathroom vanities, or outdoor furniture, film faced plywood is an excellent material. Its smooth finish is also ideal for modern, minimalist designs, aligning with the emerging industrial design trend of rustic minimalist tones by designers and specifiers in the construction of furniture and joinery creations highlighting the innate plywood strength and beauty.
- Signage and advertising boards: The smooth, paintable surface and weather resistance make it ideal for outdoor applications.
The versatility of film faced plywood means it's not just limited to construction sites. Its unique combination of properties makes it a valuable material across diverse industries.
7. Understanding the Grades and Core Veneer Options: Birch vs. Poplar Core Film Faced Plywood - Choosing the Right Core Veneer for Your Film Faced Plywood Needs
When selecting film faced plywood, understanding the different grades and core veneer options is crucial to ensure you choose the right product for your specific needs. The core veneer, the inner layers of wood that make up the bulk of the plywood, significantly impacts its strength, durability, and overall performance. Two common core veneer options are birch and poplar.
-
Birch Core Film Faced Plywood: Birch core plywood is known for its superior strength and durability. Birch is a dense hardwood, resulting in a plywood that is exceptionally strong, rigid, and resistant to impact. Birch core formply is often preferred for applications demanding high structural integrity and multiple reuses in concrete formwork, sometimes achieving plywood: 16-40 times of reuse. While typically more expensive, the longevity and performance of birch core plywood often justify the investment for demanding projects.
-
Poplar Core Film Faced Plywood: Poplar core is a more economical option. Poplar is a softer wood, making poplar core plywood lighter and more flexible than birch core plywood. While not as strong or durable as birch, poplar core formply is still suitable for many concrete formwork applications, especially those with fewer reuses required (formply: 1-19 times). It's a making it a cost-effective choice for projects where budget is a primary concern, or for applications where extreme durability is not paramount.
The choice between birch and poplar core depends on the project's specific requirements. For heavy-duty applications and maximum reusability, birch core plywood is the superior choice. For less demanding applications or budget-conscious projects, poplar core may suffice.
8. Why Choose LVL Film Faced Plywood for Enhanced Strength and Stability? - Exploring the Benefits of LVL Core in Film Faced Plywood
For applications requiring the ultimate in strength and stability, LVL (Laminated Veneer Lumber) core film faced plywood presents a premium solution. LVL timber is an engineered wood product created by layering thin wood veneers in parallel and bonding them together with adhesive. This process results in a material with significantly enhanced strength and durability compared to solid sawn timber or standard plywood cores.
When LVL is used as the core material for film faced plywood, the result is a product with exceptional load-bearing capacity, dimensional stability, and resistance to warping and twisting. LVL core formply is ideal for demanding concrete formwork applications, particularly for complex shapes or high-pressure pours. The consistent quality and strength of LVL ensure reliable performance and extended lifespan, even in the most challenging conditions.
Consider LVL core film faced plywood when your project demands:
- Maximum strength and stiffness
- Superior dimensional stability
- Resistance to heavy loads and pressures
- Minimal deflection or deformation under stress
- Extended lifespan and reusability
While LVL core film faced plywood may represent a higher initial investment, its enhanced performance and longevity often translate to long-term cost savings and improved project outcomes, especially in structural applications. We, at JSY LVL, specialize in engineered wood products like LVL, and can attest to its superior performance in demanding construction environments. Explore our range of LVL Timber (Engineered Wood Products) to learn more about the benefits of LVL in construction.
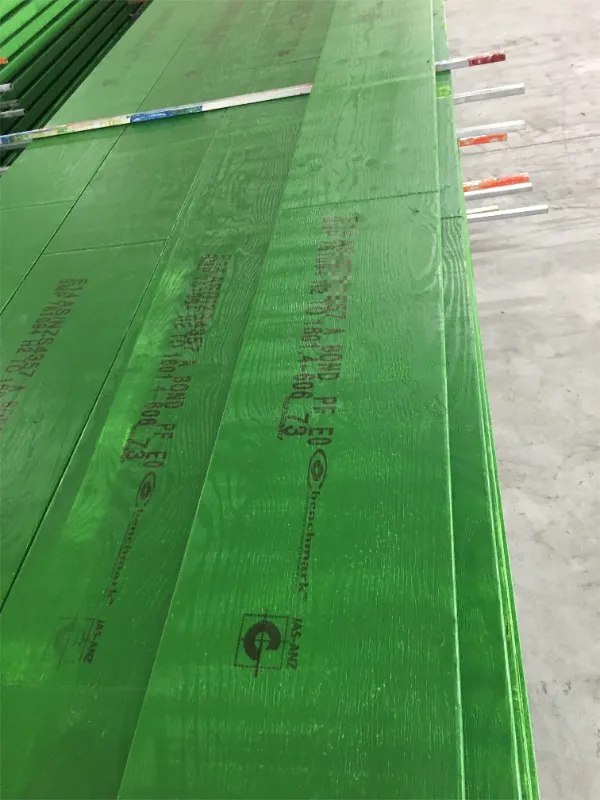
LVL Timber, providing enhanced strength for demanding applications.
9. Meeting Australian Standards: Ensuring Quality and Compliance with Formply - Understanding Formply Standards and Certifications
In Australia, and many other regions, formply used in concrete formwork must adhere to specific standards to ensure safety, durability, and performance. Australian Standard AS/NZS 6669:2018, "Plywood – Formwork," sets out the requirements for formply sheets intended for use in concrete formwork. This standard covers aspects such as:
- Plywood construction and veneer quality
- Bonding quality and adhesive type
- Film face properties and adhesion
- Dimensional tolerances and squareness
- Marking and labeling requirements
Compliance with Australian Standard 6669 is a critical factor when selecting formply, particularly for structural concrete formwork applications. Using certified formply provides assurance of quality and strength, ensuring that the material will perform reliably and safely under the stresses of concrete form. When sourcing formply, always ask your supplier for documentation demonstrating compliance with relevant standards, such as AS/NZS 6669 in Australia. This ensures you are using certified plywood is not required but high-quality materials that meet industry benchmarks for performance and safety.
10. Where to Buy High-Quality Film Faced Plywood and Formply from a Trusted Supplier in China? - Sourcing Reliable Film Faced Plywood and Formply from JSY LVL
Sourcing high-quality film faced plywood and formply from a reliable supplier is paramount to ensuring the success of your construction or manufacturing projects. As a leading factory in China specializing in engineered wood products, JSY LVL is your trusted partner for premium film faced plywood, formply, and other building materials.
With multiple production lines and a focus on quality control, we offer a comprehensive range of film faced plywood products to meet diverse needs:
- Various thicknesses: From 9mm to 25mm and beyond, including popular sizes like 12mm 15mm 18mm film faced plywood construction building formwork Poplar eucalyptus pine.
- Core veneer options: Poplar, eucalyptus, birch core plywood, and LVL core available.
- Film face colors: Black, brown, and other colors upon request.
- Standard sizes: 2400 x 1200mm sheets, 1800 x 1200mm sheets, and custom sizes.
- Grades: Meeting F11, F17, and F27 structural plywood requirements, as well as non-structural options.
We export our film faced plywood and formply globally, with a strong presence in the USA, North America, Europe, and Australia. We understand the key concerns of buyers like Mark Thompson – quality inspection, certifications, dimensional accuracy, and reliable logistics. We are committed to providing:
- Consistent quality: Rigorous quality control processes ensure consistent grade, moisture content, and lamination quality across every batch.
- Certifications: We can provide necessary certifications such as FSC, CARB compliance, and structural plywood certifications upon request.
- Dimensional accuracy: Our precision manufacturing ensures accurate dimensions for easy installation and consistent concrete formwork.
- Timely delivery: Efficient logistics and streamlined production processes ensure on-time shipments to meet your project schedules.
- Competitive pricing: We offer cost-effective solutions without compromising on quality.
Whether you are a construction company, building material supplier, formwork contractor, or furniture manufacturer, JSY LVL is ready to meet your film faced plywood and formply needs. Contact us today to discuss your project requirements and request a quote. We are confident that our high-quality products and reliable service will make us your preferred supplier for engineered wood products. You can also explore our website to view our full range of products, including Structural Plywood and Non-Structural Plywood.
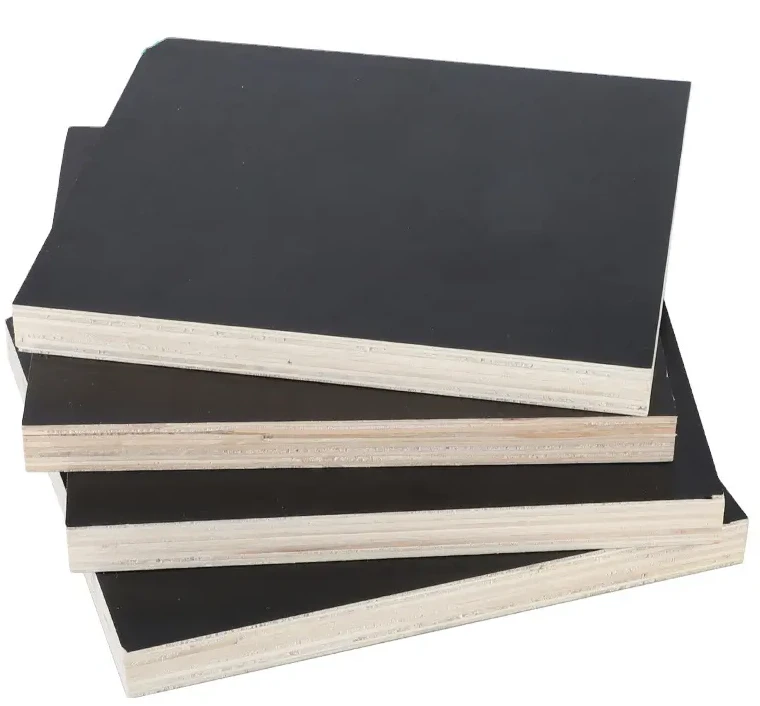
Poplar core film faced plywood, a cost-effective option.
Key Takeaways:
- Film faced plywood (formply) is a waterproof, durable plywood with a phenolic film or melamine coating, ideal for concrete formwork and high-wear applications.
- Formply is essentially film faced plywood specifically designed for concrete formwork, known for its reusability (formply: 1-19 times, high-grade up to plywood: 16-40 times).
- Film faced plywood is more water-resistant and durable than regular plywood due to its film coating and phenolic resin bonding.
- Beyond concrete formwork, film faced plywood is versatile for flooring, scaffolding, vehicle building, furniture, and more.
- Core veneer options like birch core plywood offer superior strength and durability, while poplar core provides a more cost-effective alternative.
- LVL core film faced plywood offers enhanced strength and stability for demanding structural applications.
- Always ensure formply complies with relevant standards like Australian Standard 6669 for formwork plywood.
- JSY LVL in China is a trusted supplier of high-quality film faced plywood and formply, offering various options and reliable service for global B2B customers.
Post time: Feb-21-2025